Traveling Head Press
Manufacturer&Supplier
38+ Years
Top European Quality
100% Factory Price
Excellent service
Free Installstion&Traning
Your Trusted Partner for Traveling Head Press
With over 38 years of industry experience, Gerson is a leading manufacturer specializing in high-quality traveling head presses and innovative die-cutting machinery. We serve a wide range of clients, from individual entrepreneurs to large corporations, ensuring exceptional quality and customer satisfaction.
Drawing on our extensive technical knowledge and rich history in production, Gerson provides customized solutions tailored to your specific requirements. Whether you need standard machinery or custom-built options, our dedicated team is focused on delivering excellence in every project.
Contact us today to explore how Gerson can elevate your production capabilities.
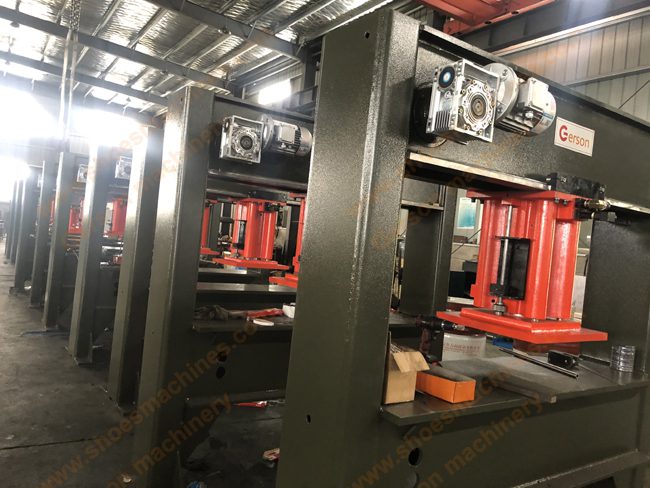
Gerson Manual Traveling Head Press
GRM Manual Traveling Head Press
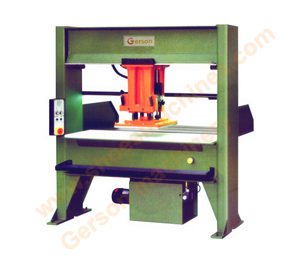
Main Features & Specification :
Manual traveling head press is one of die cutting press machine with traveling head .It is manual feeding material in sheet or roll form to die cut out small or medium shapes by normal cutting die.
Cutitng Force: From 25 tons to 200 tons.
Working Table Size: 1600X500,1600X600,1800X500,2200X500mm etc.,(Custom build)
Movable head: 500X500mm,600X600mm 750X750 etc.,
Gerson Automatic Traveling Head Press
GRMA Automatic Traveling Head Press
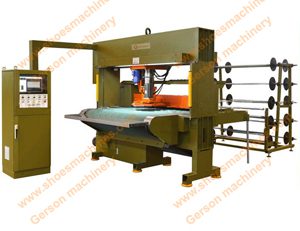
Main Features & Specification :
Automatic traveling head press is automatic feeding material continuous die cut out required shaped from sheet or roll form by normal cutting die.It can be CNC traveling head press and equiped with other automatic machinery.
Cutitng Force: From 25 tons to 200 tons.
Working Table Size: 1600X500,1600X600,1800X500,2200X500mm etc.,(Custom build)
Movable head: 500X500mm,600X600mm 750X750 etc.,
Related Products with Traveling Head Press
Gerson Swing Arm Clicker Press is entry lever hydraulic die cutting press for soft and semi-rigid material .It is for cutting out small and medium material by normal cutting dies in Small batch production.
Gerson Full Beam Press is one of hydraulic presses for punching out from small ,medium,large shapes from large material .CNC Automatic beam press machine can spped up the production capacity.
Desktop clicker press
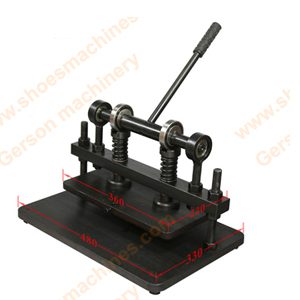
Gerson desktop Clicker Press is mini type hand operated die cutter machine. It is widely used in small shop or home or lab for cutting out non-metal components of small material .High quality &low cost.
Traveling Head Press: Ultimate Guide
(keep updating: Updated on Nov 09th, 2024.)
Traveling Head Press: Ultimate Guide
What is a Trveling Head Press?
Traveling Head Press Overview
A Traveling Head Press, also referred to as a traveling head cutting press or traveling head cutting machine, is a type of die-cutting press designed for efficiency in processing wide sheets or roll materials. This machine features a movable upper platen or beam that can travel horizontally (left or right), allowing for versatile operation.
Hydraulic System Functionality
The Traveling Head Press utilizes a hydraulic system to generate the necessary hydraulic pressure for its operations. This system is crucial as it enables the press to exert significant force on the material being cut, ensuring precise and clean cuts.
Movement Mechanism
The movement of the traveling head is motorized and driven by a chain and sprocket mechanism. This allows for both manual and automatic operation modes, providing flexibility depending on production needs. The automatic models are particularly advantageous for high-volume production environments where efficiency is paramount.
What Materials can be Used for the Traveling Head Press?
Traveling head presses are highly versatile machines designed to cut a wide range of materials, from soft fabrics to semi-rigid plastics. They are commonly used in industries such as apparel, footwear, automotive, electronics, and packaging.
Materials Commonly Processed:
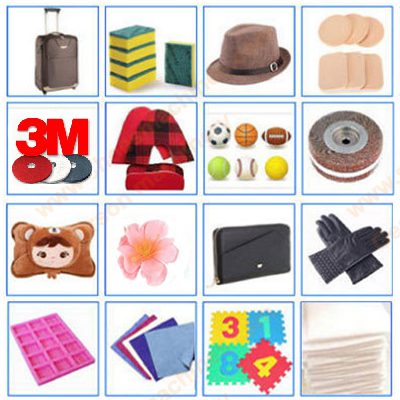
- Soft Materials: Leather (natural, PU, artificial), fabric, paper, cardboard
- Semi-Rigid Materials: Aluminum foil, copper foil, foam (polyester, polyurethane, polyether, polyethylene, rubber, silicone, neoprene, nitrile rubber, EPDM, EFO, EPOM, EVA, fluorosilicone), Mylar, Lexan, Formex, styrene, polyimide (Kapton), PTFE (Teflon), UHMW polyethylene
Gerson: Custom Die Cutting Solutions
Gerson specializes in designing and manufacturing custom die-cutting machines tailored to specific material and production needs. Whether you’re working with soft or rigid materials, Gerson can provide a customized solution to optimize your cutting process.
In Conclusion
Traveling head presses are a valuable asset for businesses that require precise and efficient cutting operations. With Gerson’s expertise in custom machine design, you can ensure that your die-cutting needs are met with the highest level of precision and productivity.
Is Traveling Head Press Same as Clicker Press ?
A traveling head press is a type of clicker press, a category of die-cutting machines that use a cutting blade to cut materials. While clicker presses come in various configurations, including swing arm, traveling head, and full beam, the traveling head press is distinguished by its moving cutting head that travels along a track to cut large sheets or roll of material.
Traveling Head Press: A Specialized Clicker Press
- Clicker Press: A broad category of die-cutting machines that use a cutting blade to cut materials.
- Traveling Head Press: A specific type of clicker press where the cutting head moves along a track to cut large sheets or roll of material.
To delve deeper into the world of clicker presses and their applications, we encourage you to explore specialized resources., you will learn a lot from:Clicker Press Knowledge
How a Traveling Head Press Works?
Operating a Traveling Head Press: A Basic Guide
Operating a traveling head press involves understanding its components, safety features, and operational procedures. Here’s a step-by-step guide to effectively operate this machinery.
1. Understanding the Machine Components
Before operating the traveling head press, familiarize yourself with its main components:
- Cutting Platen: This is where the material is placed for cutting. It is motorized and driven by a chain and sprocket system.
- Cutting Die: The tool that shapes the material during the cutting process.
- Cutting Table: The platform where the material is placed for cutting.
- Control Panel: Used to adjust machine settings, such as cutting pressure, speed, and head position.
- Head Movement Controls: The machine allows for manual or automatic left-right movement of the cutting head.
- Push-button Controls: These controls are essential for operating the machine safely. They include two-hand push buttons that ensure both hands are engaged during operation.
- Hydraulic System: This system provides the necessary pressure to cut through materials effectively.
2.Safety Precautions
- Operator Training: Ensure operators are properly trained on machine operation and safety procedures.
- Two-Hand Control: Always use both hands on the control buttons to prevent accidental activation.
- Personal Protective Equipment (PPE): Wear safety glasses, gloves, and other appropriate protective gear.
- Machine Guards: Ensure all safety guards are in place to prevent accidental contact with moving parts.
- Regular Maintenance: Perform routine maintenance to keep the machine in optimal condition.
3. Preparing for Operation(Before starting the machine)
- Inspect the Machine: Check for any visible damage or wear on components. Ensure that all safety features are functional.
- Material Setup: Place your synthetic material (either in roll or sheet form) securely on the cutting platen. Make sure it is aligned correctly according to your cutting specifications.
- Select Cutting Tool: Choose an appropriate die for your desired shape and place it on the material.
4.Operating Procedures
Machine Setup (Before Starting):
- Inspection: Check for visible damage or wear on components. Verify that all safety features function correctly.
- Material Setup: Secure the synthetic material (roll or sheet) on the cutting platen, aligning it with your cutting specifications.
- Cutting Tool Selection: Choose the appropriate die for your desired shape and place it on the material.
Cutting Process:
(a) Manual Traveling Head Press:
- Position the cutting head over the desired cutting area.
- Engage the cutting mechanism to apply pressure and cut the material.
- Move the cutting head to the next cutting position and repeat the process.
(b) Automated Traveling Head Press (e.g., Gerson):
- Automatic Roll Feed: Continuously feeds material into the cutting area.
- Continuous Cutting: Enables uninterrupted production.
- Precise Cutting: Ensures accurate and efficient cuts.
Material Advancement:
- Manually or automatically advance the material to the next cutting position.
- Repeat the cutting process for subsequent cuts.
Machine Monitoring:
- Keep an eye on the machine’s performance, including the cutting head movement, hydraulic pressure, and overall operation.
- Listen for any unusual noises or vibrations that may indicate a problem.
Machine Shutdown:
- Once cutting is complete, turn off the machine and disconnect the power supply.
- Clean the machine and its components to remove any debris or material.
Refer to the provided Gerson instruction manual for specific operating procedures and safety guidelines.
Cutting Video Reference:
The provided video demonstrates continuous cutting with automatic roll feed material (link can be inserted here).
Which Industries are Traveling Head Presses Used in?
Traveling Head Presses are versatile machines utilized across a wide range of industries due to their ability to handle complex cutting tasks efficiently. Here’s a detailed breakdown of the primary industries that benefit from these machines:
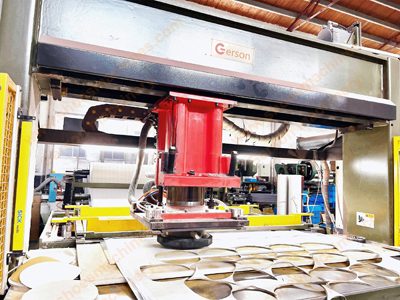
Textile and Apparel
- Clothing: Cutting components for hats, ties, collars, and shoulder pads.
- Footwear: Producing shoe uppers, insoles, and straps.
- Textiles: Creating sample swatches, pattern books, and various textile products.
Packaging and Labeling
- Packaging: Cutting foam inserts, cardboards, and promotional materials.
- Labels: Producing labels for various products, including clothing, electronics, and food.
Automotive and Aerospace
- Gaskets and Seals: Cutting precise gaskets and seals for automotive and aerospace components.
- Insulation Materials: Producing insulation components for vehicles and aircraft.
Medical and Healthcare
- Medical Devices: Cutting components for medical devices, such as filters, dressings, and orthopedic footwear.
- Pharmaceutical Packaging: Cutting blister packs and other packaging materials.
Electronics
- Circuit Boards: Cutting flexible PCBs and other electronic components.
- Keypads and Buttons: Producing keypads, buttons, and other user interface elements.
Other Industries
- Industrial Materials: Cutting gaskets, seals, washers, and filters made from various materials like rubber, plastic, and felt.
- Construction: Cutting insulation materials and other construction components.
- Consumer Goods: Cutting components for toys, games, and household items.
By understanding the diverse applications of traveling head presses, businesses can leverage these machines to enhance productivity, improve product quality, and reduce costs.
What Kind of Die Tools can be Used on Traveling Head Press ?
Traveling head presses are versatile machines that utilize various types of cutting die tools to efficiently cut materials. Here are some common types,Gerson can custom built any below cutting die for your traveling head press:
1. Steel Rule Dies
- Widely used: Versatile and cost-effective.
- Precision Cutting: Ideal for intricate shapes and patterns.
- Material Compatibility: Suitable for paper, cardboard, and soft plastics.
2. Pre-Sharpened Dies (Clicker Dies)
- Ready-to-Use: Pre-sharpened for immediate use.
- Clean Cuts: Ensures precise and clean cuts.
- Material Compatibility: Suitable for leather, fabric, and other soft materials.
3. Forged Dies
- Durability: Built to withstand heavy-duty cutting tasks.
- High-Pressure Applications: Ideal for thick or tough materials.
- Long-Lasting: Offers extended lifespan due to its robust construction.
By understanding the characteristics and applications of these cutting die tools, you can select the most appropriate option for your specific cutting needs, optimizing the performance of your traveling head press.
What Types of Traveling Head Presses are There ?
Traveling head presses are versatile machines used in various industries for cutting materials like leather, fabric, and paper. They come in different types and specifications to accommodate diverse production needs.
Types of Traveling Head Presses
Manual Feed Traveling Head Press:
- Requires manual placement and feeding of materials.
- Suitable for smaller operations or jobs requiring flexibility.
Automatic Feed Traveling Head Press:
- Uses automated systems for material feeding.
- Handles sheet and roll materials.
- Ideal for large-scale production.
Cutting Pressure Specifications
Traveling head presses are categorized based on their maximum cutting pressure:
- 30 Ton
- 35 Ton
- 40 Ton
- 50 Ton
- 100 Ton
- 120 ton
- 150 ton
The appropriate cutting pressure depends on the material thickness and the complexity of the cutting operation. Higher tonnage presses are suitable for thicker materials and more demanding cutting tasks.
By understanding these types and specifications, you can select the most suitable traveling head press for your specific production requirements.
What is a Swing Arm Clicker Press ?
A Swing Arm Clicker Press is clicking press with swing arm or beam.in fact ,It is using a electro-hydraulic to generate a compressive force to die-cut soft and semi-rigid material.It is first entry hydraulic cutting press used in shoes industry.So you will hear hydraulic swing arm cutting machine which high probability refers to hydraulic clicker press.
For more information ,we recommend the read below :Swing Arm Clicker Press: Definitive Guide
What is a Manual Traveling Head Press ?
A Manual Traveling Head Press is a versatile die-cutting machine that offers precise and efficient cutting of a wide range of materials, including leather, rubber, foam, textiles, and non-ferrous substrates.
Key Features and Operation:
- Manual Operation: Operators manually position the material, set the cutting head, and initiate the cutting process.
- Cutting Capacity: Handles materials up to 80 inches wide, with custom options available for larger rolls.
- Tonnage Options: Available in various tonnage capacities (25-100 tons) to accommodate different material thicknesses.
- Safety Features: Equipped with two-hand safety controls to prevent accidents.
- Versatility: Suitable for intricate cutting patterns and smaller production runs.
Applications:
Manual Traveling Head Presses are ideal for industries that require:
- Precision Cutting: For detailed and intricate designs.
- Small-Scale Production: For lower-volume production runs.
- Material Versatility: For cutting a wide range of materials, from soft to semi-rigid.
- Custom Designs: For unique and customized cutting patterns.
Feature | Benefit |
---|---|
Manual Operation | Operator control for precise and customized cuts |
Cutting Capacity | Handles wide materials, up to 80 inches |
Tonnage Options | Accommodates various material thicknesses |
Safety Features | Ensures operator safety with two-hand controls |
Versatility | Suitable for intricate designs and small-scale production |
By providing a combination of manual control and powerful cutting capabilities, manual traveling head presses offer a flexible and efficient solution for various cutting needs.
What is a Automatic Traveling Head Press ?
An automatic traveling head press is a highly efficient die-cutting machine designed to automate the cutting process for various materials, including leather, rubber, foam, textiles, and non-ferrous substrates.
Key Features:
- Traveling Head Mechanism: A movable cutting head that travels across the material, ensuring precise cuts.
- Automation: Minimizes manual intervention, increasing productivity and reducing operator error.
- High-Speed Cutting: Capable of high-speed cutting, often exceeding 100 cuts per minute.
- Energy Efficiency: Utilizes energy-efficient technologies like servo-driven systems to reduce power consumption and maintenance.
- Advanced Nesting Software: Optimizes material usage by calculating efficient cutting patterns.
- Robotic Integration: Can be integrated with robots for automated material handling and part removal.
- Safety Features: Equipped with safety features like two-hand controls to prevent accidents.
Benefits of Automatic Traveling Head Presses:
- Increased Productivity: High-speed cutting and automated processes boost output.
- Improved Precision: Ensures consistent and accurate cuts.
- Reduced Labor Costs: Minimizes manual labor requirements.
- Optimized Material Usage: Nesting software reduces material waste.
- Enhanced Safety: Built-in safety features protect operators.
Feature | Benefit |
---|---|
Traveling Head Mechanism | Increased flexibility and accessibility |
Automation | Reduced manual labor, improved efficiency |
High-Speed Cutting | Increased productivity |
Energy Efficiency | Lower operating costs, reduced environmental impact |
Advanced Nesting Software | Optimized material usage, reduced waste |
Robotic Integration | Further automation, increased efficiency |
Safety Features | Enhanced operator safety |
In summary, an automatic traveling head press is a highly efficient and versatile machine designed for precise die cutting operations in industrial settings. Its combination of automation, speed, energy efficiency, and advanced technology makes it an essential tool in modern manufacturing processes.By understanding the key features and benefits of automatic traveling head presses, you can make informed decisions about their suitability for your specific production needs.
Which is the Best ? Swing Arm Clicker Press VS Manual Traveling Head Press?
When choosing between a Swing Arm Clicker Press and a Manual Traveling Head Press, several factors must be considered. Here’s a breakdown of their key differences:
Working Area:
- Swing Arm Clicker Press: Limited working area, typically around 1200mm x 500mm.
- Manual Traveling Head Press: Offers a larger working area, ranging from 1600mm x 600mm to 2500mm x 750mm or more. This makes it suitable for wider materials and larger die cuts.
Cutting Pressure:
- Swing Arm Clicker Press: Typically has a maximum pressure of around 30 tons.
- Manual Traveling Head Press: Offers higher pressure capabilities, ranging from 25 tons to 150 tons or more. This allows for cutting thicker and more resistant materials.
Upper Pressing Plate:
- Swing Arm Clicker Press: Limited movement, typically left and right, and a smaller maximum width.
- Manual Traveling Head Press: Offers greater flexibility with wider movement and larger upper pressing plates.
Versatility:
- Swing Arm Clicker Press:
- Simpler operation, suitable for basic shapes and smaller production runs.
- Limited range of motion and reliance on manual positioning can affect efficiency for complex cuts or larger sheets.
- Manual Traveling Head Press:
- Offers greater flexibility with adjustable head movement for intricate cuts and larger sheets.
- Can be more efficient for complex patterns and higher production volumes.
- Can be customized with features like heated platens for specific applications.
Ease of Use:
- Swing Arm Clicker Press:
- Relatively simple operation.
- Requires manual material positioning for each cut.
- Manual Traveling Head Press:
- May require more initial setup and training.
- Offers more efficient operation once set up, especially for repetitive cuts.
Safety Features:
- Swing Arm Clicker Press:
- Basic safety features like guards and emergency stops.
- Manual Traveling Head Press:
- Often equipped with advanced safety features like light curtains and automatic die clamping systems.
Cost:
- Swing Arm Clicker Press:
- Lower initial cost, suitable for smaller budgets or basic operations.
- Manual Traveling Head Press:
- Higher initial cost but can offer long-term savings through increased efficiency and versatility.
Feature | Swing Arm Clicker Press | Manual Traveling Head Press |
---|---|---|
Working Area | Limited (around 1200mm x 500mm) | Larger (1600mm x 600mm to 2500mm x 750mm or more) |
Cutting Pressure | Lower (typically around 30 tons) | Higher (25-150 tons or more) |
Upper Pressing Plate | Limited movement, smaller maximum width | Greater flexibility, wider movement, larger upper pressing plates |
Versatility | Suitable for basic shapes and smaller production runs | Handles wider materials, thicker materials, and complex shapes |
Ease of Use | Simpler operation, but manual material positioning | May require more initial setup, but offers more efficient operation, especially for repetitive cuts |
Safety Features | Basic safety features | Often equipped with advanced safety features |
Cost | Lower initial cost | Higher initial cost but can offer long-term savings |
Conclusion:
The best choice between a Swing Arm Clicker Press and a Manual Traveling Head Press depends on your specific needs. Consider the following factors:
- Material Types and Thicknesses: If you work with a variety of materials and thicknesses, a Manual Traveling Head Press is more versatile.
- Cutting Complexity: For simple shapes, a Swing Arm Clicker Press may suffice. For intricate designs, a Manual Traveling Head Press is better suited.
- Production Volume: For high-volume production, a Manual Traveling Head Press can be more efficient.
- Budget: Consider the initial cost and long-term savings of each option.
By carefully evaluating these factors, you can select the right machine to optimize your production process.
How to Choose Traveling Head Press ? Manual or Normal Autoamtic or CNC ?
When selecting a traveling head press, it’s essential to consider several factors that will influence your decision between manual, automatic, or CNC options. Here’s a step-by-step breakdown of how to make the best choice for your specific needs.
1. Production Volume and Complexity
- Manual Presses: Suitable for low-volume production and simple cuts.
- Automatic Presses: Ideal for medium-volume production and more complex cutting tasks.
- CNC Presses: Best for high-volume production and intricate designs.
2. Material Types and Sizes
- Material Compatibility: Ensure the press can handle your specific materials (e.g., leather, fabric, foam).
- Size Requirements: Consider the maximum material size you’ll be cutting.
3. Automation Level
- Manual: Requires manual material handling and cutting.
- Semi-Automatic: Offers partial automation, reducing manual labor.
- Fully Automated (CNC): Provides maximum automation, precision, and efficiency.
4. Safety Features
- Essential Safety Features: Light curtains, emergency stop buttons, and automatic die clamping systems.
5. Budget
- Initial Cost: Manual presses are generally less expensive than automatic or CNC models.
- Long-Term Costs: Consider factors like maintenance, energy consumption, and labor costs.
Feature | Manual Traveling Head Press | Normal Automatic | CNC Traveling Head Press |
---|---|---|---|
Production Volume | Low to Medium | Medium to High | High |
Complexity of Cuts | Simple to Moderate | Moderate to Complex | Complex |
Automation Level | Manual | Semi-Automated | Fully Automated |
Material Handling | Manual | Automated Feeding Systems | Automated Feeding and Nesting |
Precision | Moderate | High | Very High |
Initial Cost | Lower | Medium | Higher |
Long-Term Cost | Higher (due to labor) | Medium | Lower (due to automation and efficiency) |
Key Considerations:
- Precision: CNC presses offer the highest level of precision.
- Efficiency: Automated presses increase productivity.
- Flexibility: Manual presses offer more flexibility for smaller-scale operations.
- Safety: Prioritize safety features in all types of presses.
By carefully evaluating these factors, you can select the most suitable traveling head press for your specific needs.
What are The Similarities Between Traveling Head Press and Beam Press?
While these two types of presses have distinct characteristics, they share several fundamental similarities:
Core Function:
- Die-Cutting: Both are designed to cut various materials using dies.
- Material Handling: Both can handle sheet and roll materials, though specific feeding systems may vary.
Mechanical Operation:
- Hydraulic Power: Both rely on hydraulic power to apply pressure to the cutting die.
- Cutting Process: Both involve a cutting die that shapes the material under pressure.
Safety Features:
- Operator Protection: Both are equipped with safety features like emergency stop buttons and light curtains.
- Maintenance Requirements: Both require regular maintenance, including lubrication and inspection.
Production Efficiency:
- High-Speed Operation: Both can achieve high production rates with proper setup and maintenance.
- Precision Cutting: Both are capable of precise cutting, ensuring consistent quality.
Feature | Traveling Head Press | Beam Press |
---|---|---|
Primary Function | Die-cutting | Die-cutting |
Material Handling | Versatile | Versatile |
Cutting Mechanism | Hydraulically powered cutting head | Hydraulically powered cutting ram |
Safety Features | Emergency stop buttons, light curtains | Emergency stop buttons, light curtains |
Maintenance | Regular lubrication and inspection | Regular lubrication and inspection |
By understanding these similarities, you can better appreciate the versatility and effectiveness of both Traveling Head Presses and Beam Presses in various manufacturing applications.
What is the Difference Between Traveling Head Press and Fixed Beam Press?
Both Traveling Head Presses and Beam Presses are essential tools in the manufacturing industry, used for cutting various materials with precision. However, they differ in their design, capabilities, and applications. About the beam press ,Your could see more details about beam press:Beam Press:The Ultimate FAQ Guide
1. Design and Operation
The Traveling Head Press features a cutting head that moves horizontally after each cut, allowing the operator to reposition the material or tooling easily for subsequent cuts. This design is particularly advantageous for cutting multiple shapes from rolls or sheets of material, as it provides flexibility in operation without requiring extensive manual adjustments.
In contrast, the Beam Press has a fixed beam where the cutting head only moves vertically. The material must be manually positioned under the cutting head using various feeding systems such as slide-in tables or roller drives. This design is more suited for high-volume production where consistent positioning of materials is required.
2. Cutting Capacity and Force
Traveling Head Presses typically range from 20 to 80 tons of cutting force, making them versatile for both low and high production capacities. They are designed to handle a variety of materials efficiently, including foam, felt, plastic films, and more.
Beam Presses have a broader range of cutting forces available, from 25 tons up to 500 tons or more. This allows them to tackle heavier and tougher materials with greater precision and power, making them ideal for industrial applications that require robust performance.
3. Material Handling
The Traveling Head Press is designed for maximum flexibility when handling both roll and sheet materials. Its ability to move the cutting head laterally reduces operator fatigue and enhances visibility during operation.
On the other hand, Beam Presses often utilize various feed systems tailored for specific applications. These can include manual or automatic systems that facilitate efficient handling of large volumes of material but may require more setup time compared to the simplicity offered by Traveling Head Presses.
4. Application Suitability
Traveling Head Presses are well-suited for operations that require frequent changes in tooling or shapes being cut due to their ease of operation and quick adjustments between cuts. They are ideal for industries where versatility is key.
Beam Presses excel in environments where high-volume production is necessary, particularly when working with larger dies or complex tooling setups that benefit from their fixed beam design and higher force capabilities.
5. Maintenance and Support
Both types of presses offer reliability; however, Traveling Head Presses are often noted for their straightforward operation which can lead to reduced maintenance needs over time due to fewer moving parts involved in repositioning tools.
Beam Presses may require more maintenance due to their complex feeding systems and higher operational demands but also provide advanced features like LVDT transducers for depth control which enhance accuracy during long-term use.
Key Differences:
Feature | Traveling Head Press | Beam Press |
---|---|---|
Design | Moving cutting head | Fixed beam |
Material Handling | Versatile, handles both roll and sheet materials | Often requires specific feeding systems for roll or sheet materials |
Cutting Force | Ranging from 20 to 150 tons | Ranging from 25 to 500 tons or more |
Application | Suitable for frequent tooling changes and diverse shapes | Ideal for high-volume production and complex tooling setups |
Maintenance | Lower maintenance needs due to simpler design | May require more maintenance for complex feeding systems |
In essence:
- Traveling Head Press: Offers flexibility and ease of operation, making it suitable for diverse applications and frequent tooling changes.
- Beam Press: Provides higher cutting forces and is optimized for high-volume production, especially for consistent, repetitive cuts.
Choosing the Right Press:
The optimal choice between a Traveling Head Press and a Beam Press depends on specific production requirements, including:
- Material Type and Thickness: Beam presses are better suited for thicker materials and higher cutting forces.
- Production Volume: High-volume production often benefits from the efficiency of beam presses.
- Cutting Complexity: Traveling head presses offer more flexibility for intricate shapes and frequent tooling changes.
- Operator Skill Level: Beam presses may require more operator skill and experience.
By carefully considering these factors, you can select the most appropriate press for your specific needs.
Why do You Need a Traveling Head Press ?
A Traveling Head Press offers a compelling combination of power, efficiency, and user-friendliness, making it a valuable asset for various industries. Here’s a breakdown of its key benefits, incorporating the information you provided:
Enhanced Performance and Stability:
- Reliable Hydraulic Power: The hydraulic driver ensures consistent operation with low noise and energy consumption (stable and reliable: Hydraulic driver guarantees stability, low consumption and low noise of performance).
Large Material Handling:
- Wide Work Area: The expansive table allows for efficient cutting of large sheets or rolls of material (For large material: Traveling Head Press Have A Wide Table can be used for cutting processing of wide materials).
Safety and Productivity:
- Operator Safety: Manual models provide a wide line of sight for clear observation of the cutting process (Wide sight and highly outpit: Manual Type Press has a wide line of sight to ensure the safety of workers cut).
- High-Yield Cutting: Both manual and automatic options offer precise cutting, maximizing material output (Wide sight and highly outpit: And fully automatic cutting to ensure high yield output).
Simplified Operation:
- Minimal Training Required: The intuitive design allows for quick setup and operation, even for users with limited experience (NO Experience Needed: Extremely easy to operate, there is almost no special training).
Feature | Benefit |
---|---|
Versatility | Handles a wide range of materials and shapes |
Efficiency | Automated options for increased productivity |
Safety | Built-in safety features for operator protection |
Precision | Accurate cutting for consistent results |
Durability | Robust construction for long-lasting performance |
Ease of Use | User-friendly interface and minimal training required |
Cost-Effective | Low operating costs and energy efficiency |
Additional Advantages:
- Large Material Capacity: Accommodates wide materials and large sheets.
- Stable Performance: Reliable hydraulic system ensures consistent operation.
- Customizable: Can be tailored to specific needs with various configurations.
By incorporating a Traveling Head Press into your operations, you can achieve precision cutting, improve production efficiency, and ensure operator safety – all while benefiting from a user-friendly and cost-effective solution.
What are the Advantages of Traveling Head Press?
A Traveling Head Press is a versatile and efficient machine that offers numerous benefits for various industries. Here’s a breakdown of its key advantages:
Performance and Reliability:
- Stable and Reliable Operation: The hydraulic drive system provides consistent and dependable performance, characterized by low energy consumption and minimal noise levels.
- Precise Cutting: The hydraulic system enables precise control over cutting force and speed, ensuring accurate and consistent results.
Versatility and Efficiency:
- Wide Material Handling: The expansive table accommodates a wide range of materials, including large sheets and rolls.
- High-Speed Cutting: The automatic cutting feature allows for efficient high-volume production.
- Reduced Operator Fatigue: The ergonomic design and ease of use minimize operator fatigue and improve productivity.
Safety and User-Friendliness:
- Operator Safety: The wide line of sight and safety features, such as emergency stop buttons, contribute to a safe working environment.
- Easy Operation: Minimal training required, making it accessible to operators of all skill levels.
Cost-Effective:
- Lower Maintenance Costs: Hydraulic systems are known for their reliability and low maintenance needs.
- Energy Efficiency: Reduces operational costs and environmental impact.
Advantage | Description |
---|---|
Stable and Reliable Performance | The hydraulic drive system ensures consistent operation with low energy consumption and minimal noise. This stability is crucial for precision in cutting and processing tasks. |
Suitable for Wide Width Materials | The traveling head press features a wide table that accommodates various wide materials, enhancing versatility for diverse applications in manufacturing and construction. |
Wide Sight and High Output | Designed with a broad line of sight, the manual type press improves worker safety during cutting operations. Fully automatic cutting maximizes output efficiency for high-volume production. |
No Experience Needed | Extremely easy to operate, requiring little to no specialized training, allowing operators to quickly become proficient and reducing downtime associated with training. |
Low Maintenance Requirements | Hydraulic systems generally require less maintenance than mechanical systems, reducing operational costs and minimizing unexpected breakdowns. |
Precision Control | Hydraulic drives provide precise control over speed and force, ensuring accurate cuts according to specifications, which is essential for critical tolerances. |
Safety Features | Many hydraulic presses include advanced safety features such as emergency stop buttons and protective guards to enhance workplace safety. |
Energy Efficiency | Modern hydraulic systems are designed to be energy-efficient, incorporating technologies that reduce power consumption while maintaining performance levels |
By investing in a Traveling Head Press, you can enhance your production capabilities, reduce costs, and improve overall efficiency.
What are the Disadvantages of Traveling Head Press?
While Traveling Head Presses offer numerous advantages, there are a few factors to keep in mind before investing in one:
Space Requirements:
- Larger Footprint: Compared to Swing Arm Clicker Presses, Traveling Head Presses have a larger body. Ensure you have sufficient space in your workspace to accommodate the machine comfortably. Carefully measure your available area before making a purchase.
Maintenance Needs:
- Hydraulic System: Traveling Head Presses utilize hydraulic oil for operation. Proper handling and regular maintenance of this oil are crucial. This includes using the correct type, conducting regular inspections, and following a schedule for oil replacement.
Cost Investment:
- Higher Price Point: Traveling Head Presses generally have a higher initial cost compared to smaller machines like manual die cutters or Swing Arm Clicker Presses. Carefully evaluate your budget and production needs to determine if the higher cost is justified in the long run.
Here’s a table summarizing these considerations:
Factor | Description |
---|---|
Space Requirements | Larger footprint than Swing Arm Clicker Presses. Carefully measure available space. |
Maintenance Needs | Requires proper handling and regular maintenance of hydraulic oil. |
Cost Investment | Higher cost compared to smaller machines. Weigh initial cost against long-term benefits. |
It’s essential to weigh these potential drawbacks against the benefits of a Traveling Head Press to determine if it’s the right choice for your specific needs. By carefully considering your production requirements, budget, and available space, you can make an informed decision.
How Do You Choose a Traveling Head Press?
Choose a suitable Traveling Head Press, perhaps it looks a headache and the Daunting task. However, from our experience, just remember that the following three points can be:
1. Requirements for production capacity: How much production production do you want to achieve? This will decide what to choose. Manual or automatic.
2.Cutting pressure: How much pressure is required for your material? It depends on the massial, cutting Die Size, Material Thickness etc.,
3.Size: Material size and cutting die size determines the size of the machine, including work area, pressure, and so on.
If you already know, or understand, GERSON will definitely help you choose the appropriate machine. If you don’t know, it doesn’t matter, we also help you. As long as you are willing to contact us.
Do Gerson have any Traveling Head Press for Sale in Stock ?
Gerson offers a range of die-cutting solutions, including Traveling Head Presses. While we stock some standard models, such as the manual Traveling Head Press with a 30 ton ,40 ton capacity and a 1600x500mm,1600X600 working area, many of our offerings are customized to meet specific customer needs.
Key Points:
- Standard Models: We stock a limited number of standard models to ensure quick delivery for common requirements.
- Customization: Most Traveling Head Presses, as well as Swing Arm and Beam Presses, are custom-built to meet specific customer needs in terms of size, capacity, and automation level. This allows us to provide tailored solutions for various industries and applications.
By offering both standard and custom options, Gerson aims to provide flexible and efficient solutions for your die-cutting needs.
What's the Price of Traveling Head Press ?
The price of a Traveling Head Press can vary significantly based on several factors:
Machine Specifications:
- Type and Model: Manual, semi-automatic, or fully automatic models will have different price points.
- Capacity and Tonnage: The cutting force and maximum material size will impact the price.
- Automation Level: The degree of automation, including features like automatic feeding and stacking, will affect the cost.
Brand and Reputation:
- Brand Reputation: Well-established brands often command higher prices due to their reputation for quality and reliability.
Additional Features and Customization:
- Heated Platens: For working with specific materials.
- Advanced Control Systems: For precise cutting and increased efficiency.
- Custom Modifications: Tailored solutions to meet specific needs.
Manufacturing Costs:
- Material Costs: The quality and quantity of materials used in the machine’s construction.
- Labor Costs: The labor involved in manufacturing and assembling the machine.
- Research and Development Costs: Investments in research and development to improve the machine’s design and functionality.
Market Demand and Economic Factors:
- Supply and Demand: Fluctuations in market demand can affect pricing.
- Economic Conditions: Economic factors like inflation and currency exchange rates can impact the overall cost.
Factor Impact on Price Machine Type Manual, semi-automatic, or fully automatic Capacity and Tonnage Higher capacity and tonnage generally increase price Automation Level More automation features lead to higher costs Brand Reputation Well-established brands often command premium prices Customization Custom modifications and specialized features can increase costs Material Quality Higher-quality materials and components can increase the price Manufacturing Costs Labor costs, material costs, and overhead expenses influence the final price Market Demand and Economic Factors Fluctuations in supply and demand, as well as economic conditions, can impact pric
To get an accurate price quote, it’s best to consult Gerson sales team. We can provide a detailed breakdown of costs based on your specific requirements.
By considering these factors and working with Gerson, you can select a Traveling Head Press that meets your needs and budget.
Does Gerson Accept Custom built Traveling Head Press ?
Yes,Gerson has a proven track record of designing and manufacturing custom Traveling Head Presses to meet diverse industry needs. With over 38 years of experience, we offer a range of customization options to ensure optimal performance and efficiency.
Key Customization Options:
- Cutting Force: Tailor the cutting force to your specific material and application requirements, with options ranging from 25 to 200 tons.
- Working Table Size: Choose from standard sizes or request custom dimensions to accommodate your material dimensions.
- Feed Types: Select from manual, sheet, or roll feeding options to optimize your workflow.
- Special Specifications: Gerson can accommodate unique requests, such as special material handling systems or specific safety features.
By working closely with you, we can design and build a Traveling Head Press that perfectly aligns with your production goals.