Swing Arm Clicker Press
Manufacturer&Supplier
38+ Years
Top Quality Same as in Europe
Own Swing Arm Clicker Press Patents
Full Support on Installstion&Traning
Leading Swing Arm Clicker Press Manufacturer
For over 38 years, Gerson has been a leading manufacturer of Sawing Arm Clicker Presses. Our expertise extends to both OEM and our own Gerson brand, ensuring top-quality solutions for your production needs.
With nearly four decades of experience, we’ve honed our rich experience to provide customized die-cutting presses tailored to your specific requirements.
Your satisfaction, our priority. We provide cutting-edge die-cutting press machines and are dedicated to meeting the needs of businesses of all sizes.
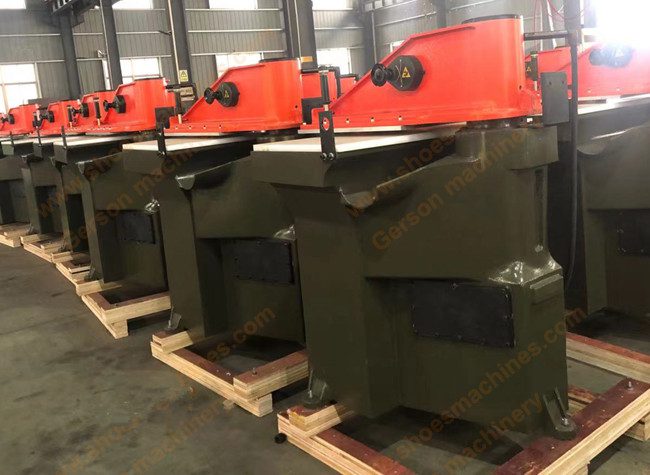
Gerson Hydraulic Swing Arm Clicker Press
Gerson GR Model Features & Specification
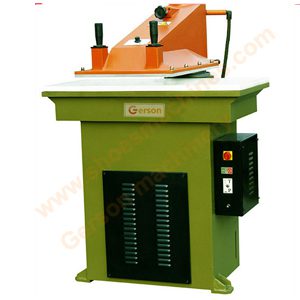
Top Design GR swing arm clicker presses offer rapid, silent operation for efficient cutting performance. Available in 20 and 27-ton models to accommodate diverse material cutting needs.
- Effortless Depth Control, Every Time.
- Versatile Cutting, Tailored to Your Needs.
- Silent Power, Precision Performance.
- See the Difference, Feel the Quality.
Model | Max. Cutting Power (Ton) | Max. Stroke (mm) | Cutting Table (mm) | Arm Width (mm) | Motor Power (HP) | Net Weight (kg) | Dimensions (mm) | Sea Packing Dimensions (mm) | Gross Weight (kg) | Volume (m³) |
---|---|---|---|---|---|---|---|---|---|---|
GR-20C | 20 | 80 | 900 x 430 | 370 | 1 | 570 | 1000 x 900 x 935 | 1050 x 1085 x 1500 | 640 | 1.7 |
GR-27C | 27 | 100 | 900 x 450 | 370 | 1.5 | 780 | 900 x 1000 x 1370 | 1050 x 1150 x 1570 | 900 | 1.90 |
GR-27C/1 | 27 | 100 | 1000 x 500 | 500/600 | 1.5 | 840 | 1000 x 1000 x 1370 | 1150 x 1150 x 1570 | 980 | 2.10 |
GR-27C/2 | 27 | 100 | 1200 x 500 | 500/600 | 1.5 | 910 | 1200 x 1030 x 1370 | 1350 x 1180 x 1570 | 1055 | 2.50 |
Gerson GRA Model Features & Specification
GRA swing arm clicker presses offer automatic stroke end setting, enabling seamless cutting with various die heights. Choose from three cutting force options to tailor your operation to any material.
- Robust Cast Iron Body Construction:A sturdy cast iron frame forms the backbone of our swing arm clicker press, ensuring longevity and reliability.
- Precise Material Placement: With a clear view of the material, you can accurately position it for cutting, minimizing errors and wasted materials.
- Simplified Operation: The unobstructed view allows for easier maneuvering of the die and material, streamlining the overall cutting process.
- Enhanced Safety: Improved visibility reduces the risk of accidents that can occur during manual cutting with limited visibility.
- Tailored to specific needs and requirements.
Model | Maximum Cutting Force (T) | Table Area (mm) | Swing Arm Width (mm) | Cutting Stroke (mm) | Motor Power (KW) | Electric Supply Voltage | Packing Size (mm) | Net Weight (kg) | Gross Weight (kg) |
GRA-220/3 | 22 | 900×430 | 370 | 90 | 1.1 | 3-Phase or Single-Phase 3×440/415/400/380/220V, 50/60Hz | 1050x1000x1500 | 650 | 740 |
GRA-270/3 | 27 | 1000×500 | 370 | 90 | 1.5 | 1150x1200x1500 | 960 | 1120 | |
GRA-270M/3 | 27 | 1000×500 | 500 | 90 | 1.5 | 1150x1200x1500 | 1050 | 1210 | |
GRA-270L/3 | 27 | 1000×500 | 610 | 90
| 1.5 | 1150x1200x1500 | 1200 | 1360 |
Gerson GSB Model Features & Specification
Our entry-level hydraulic swing arm clicker press is the perfect solution for small and medium-sized businesses. With cutting forces ranging from 8 to 30 tons, it effortlessly handles a wide variety of materials, including:
- Lightweight and Flexible Swing Arm.
- Quiet Operation and Low Maintenance.
- Adjustable Cutting Position.
- Customizable Solutions for requirements.
Model | GSB-10/12/14/15/16/18/20/25 |
Cutting Force | 10,12,14,15,16,18,20,25 Tons |
Sway Arm Width | 330X450,350X450,450X550mm |
Stroke Adjustment | 5-75mm |
Range between working table | 60-140mm |
Table Area | 900X400mm,1000X500mm |
Electric Supply Voltage | 3×440/415/400/380/220V, 50/60Hz |
Motor Power | 0.75kw,1.1kw,1.5Kw |
Packing Size(LXWXH) | 1100X1100X1700mm |
Weight | 500/650/1000/1100kg |
Hydraulic oil (46#) | 50 Liters |
Gerson Mechanical Swing Arm Clicker Press
Gerson MX Model Features & Specification
Our entry-level mechanical swing arm clicker press is the perfect tool for small-scale cutting operations. Designed for simplicity and reliability, it effortlessly handles a wide range of materials.
- Mechanical Power: Leveraging mechanical force for precise and powerful cutting.
- Versatile Applications: Suitable for cutting small to medium-sized materials.
- Durable Construction: Built to last, ensuring long-term performance.
- Easy Operation: User-friendly design for efficient workflow.
For heavier-duty cutting requirements, consider our hydraulic clicker presses. These advanced machines offer superior cutting power and versatility.
Model | MX-5T,MX-6T serials |
Max cutting force(T) | 5-6T |
Range between working table | 50-240mm (Upper to Bottom Table) |
Stroke Adjustment | 0-170mm |
Cutting table | 580×360,700×380 etc., |
Based on your material and die | |
Example: 500X400mm etc., | |
Cutting Head | 330×450 to More |
Motor power | 1.1kw,1.5kw |
Electric Power | 220V/380V/415V,50-60hz etc., |
Machine Net weight (KG) | 400 to 800 |
500 to 1000 |
Related Products with Swing Arm Clicker Press
Traveling Head Clicker Press
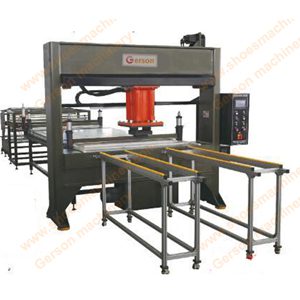
Gerson Traveling Head Clicker Press is is high lever than swing arm clicker press which have large cutting table with manual feed or can be with auto feed and continuous cutting for both sheet and roll material.
Full Beam Clicker Press
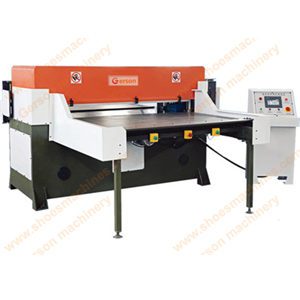
Gerson Full Beam Clicker Press is full beam or head which is for cutting out large pieces both metal or non-metal material in roll or sheet etc., in large volume production capacity.OEM or any quantity order. accept.
Tabletop clicker press
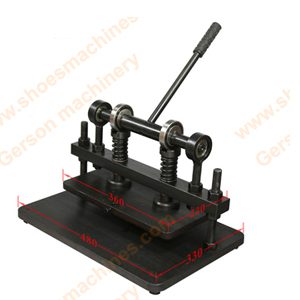
Gerson Tabletop Clicker Press is mini small size known as manual clicker press or hand operated clicker press using hand power .Die-cut out non-metal components of material with small volume at home or shop or lab.
Swing Arm Clicker Press: Definitive Guide
(keep updating: Updated on Jan. 10th, 2025.)
Swring Arm Clicker Press: Definitive Buying Guide
What is a Swing Arm Clicker Press?
The swing arm clicker press, also known as a swing beam or swing head clicker press, is a fundamental tool for punching out small and medium-sized pieces of material.It is also a classic clicker press since it was invented.The swing arm clicker press boasts a unique upper arm design. This swing arm can be effortlessly moved to the side, granting you unobstructed visibility of the material being cut. It’s considered the most basic clicker press design, and for good reason: it’s simple, reliable, and efficient.This translates to several key benefits:
Here’s what makes the swing arm clicker press a great choice:
- Easy Operation: The swing arm, or upper beam, can be easily moved aside, offering a clear view of the material you’re cutting. This allows for precise positioning and operation compared to traditional hand-cutting methods.
- Increased Efficiency: By eliminating manual cutting, the swing arm press significantly speeds up your production process.
- Classic Design: This tried-and-true technology has been around for a long time, demonstrating its effectiveness and reliability.
Ideal for:
- Hobbyists and crafters
- Small businesses
- Low-volume production
About clicker press, you could visit below for more details:
Clicker Press : Definitive Guide .This guide has all you need about clicker press.You will learn a lot from it.
What is The Swing Arm Clicker Press Used for?
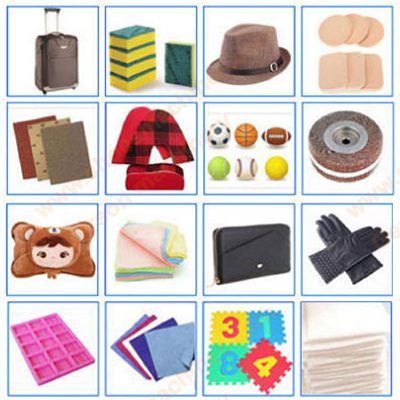
The swing arm clicker press is a versatile machine capable of cutting a wide range of soft to semi-rigid materials:
- Leather: Natural leather, PU leather, and artificial leather are commonly used for footwear, apparel, accessories, and more.
- Fabric: Textiles of various types, including cotton, polyester, nylon, and denim.
- Rubber and Plastic: Used in various industries, including automotive, manufacturing, and construction.
- Foam and Sponge: Ideal for packaging, cushioning, and insulation materials.
- Paper and Cardboard: Used in packaging, printing, and other industries.
- Cork: Commonly used for gaskets, coasters, and other products.
- Felt: Used in various applications, including crafts, upholstery, and insulation.
- Adhesives and Vinyl: Often used in signage, graphics, and automotive applications.
The specific materials that can be cut will depend on the machine’s cutting force, table size, and the type of cutting die used.This makes it an indispensable tool for various industries, including:
- Leather Processing: Cutting leather for footwear, apparel, accessories, and more.
- Textile Manufacturing: Cutting fabric for garments, upholstery, and other textile products.
- Packaging Industry: Cutting paper, cardboard, and foam for packaging solutions.
- Rubber and Plastic Industries: Cutting rubber and plastic sheets for various applications.
When was a Swing Arm Clicker Press Invented?
The swing arm clicker press, a mechanical marvel, traces its origins back to the late 18th century. Since its inception, it has been a cornerstone in various industries, particularly footwear, leather goods, and textile manufacturing.
In the early 19th century, shoe factories were among the first to adopt this innovative technology. The swing arm clicker press revolutionized the way component parts like vamps, quarters, soles, and other pieces were cut, significantly improving efficiency and precision.
Even today, the swing arm clicker press remains a popular choice for businesses of all sizes. Its simple design, reliable performance, and versatility make it a valuable asset in workshops and factories around the world.
Can the Swing Arm Clicker Press Die-cut any Shapes or Patterns ?
Swing arm clicker presses are incredibly versatile tools that can cut a wide range of shapes and patterns. The key to this versatility lies in the cutting die.
A cutting die is a precision tool that is used to create the desired shape in the material. By simply swapping out one die for another, you can easily change the shape of the cut pieces. This makes swing arm clicker presses highly adaptable to different production needs.
Whether you’re cutting simple shapes or intricate designs, the swing arm clicker press, combined with the right cutting die, can deliver precise and efficient results.
What are the types of swing arm clicker press ?
Swing arm clicker presses can be categorized based on their power source and cutting capacity:
By Power Source:
Mechanical Swing Arm Clicker Presses:
- Rely on manual or mechanical force to operate.
- Suitable for smaller-scale operations and lighter materials.
Hydraulic Swing Arm Clicker Presses:
- Utilize hydraulic power to generate significant cutting force.
- Ideal for heavier-duty applications and cutting thicker materials.
By Cutting Capacity:
Small Swing Arm Clicker Presses:
- Typically range from 5 to 10 tons of cutting force.such as 5 ton,6 ton,8 ton ,10 ton
- Suitable for small-scale operations and delicate materials.
Medium Swing Arm Clicker Presses:
- Range from 12 to 20 tons of cutting force.such as 12 ton,14/15/16/18 ton.
- Commonly used in medium-scale production environments.
Large Swing Arm Clicker Presses:
- Exceed 20 tons of cutting force,such as 22 ton,25 ton,27 ton ,28 ton ,30 tons.
- Capable of handling heavy-duty cutting tasks and thicker materials.
By understanding these classifications, you can select the right swing arm clicker press for your specific needs and ensure optimal performance.
What is a Hydraulic Clicker Press ?
Hydraulic clicker presses offer a powerful alternative to their mechanical counterparts. They utilize hydraulic cylinders to generate a compressive force that cuts through materials. This method allows for:
- Higher Cutting Force: Hydraulic presses can achieve significantly higher cutting forces compared to mechanical models. This makes them ideal for thicker or denser materials.
- Precise Control: Hydraulic systems offer precise pressure control, ensuring consistent and accurate cutting results.
- Efficiency and Speed: The hydraulic operation allows for faster cutting cycles, increasing production efficiency.
Hydraulic Clicker Press Variations:
There are three main types of hydraulic clicker presses, each suited to different applications:
- Hydraulic Swing Arm Clicker Press: Similar to the mechanical version, but with hydraulic power for increased cutting force.
- Hydraulic Traveling Head Press: Features a moveable head that positions the cutting die over the material, offering greater flexibility.
- Hydraulic Full Beam Press: The entire upper beam moves for cutting, ideal for large-scale or high-volume operations.
When to Choose Hydraulic:
Hydraulic clicker presses are a wise choice for those requiring higher cutting force or larger production volumes. They may also be preferred for cutting thicker or denser materials that require more power to penetrate. However, their higher cost and complexity compared to mechanical models should be considered.
What is a Mechanical Clicker Press ?
Mechanical clicker press is the cutting machine with mechanical transmission which is faster, stable in operation (after adjustment, the lower limit of the stroke will not change), and the punching force is large; its biggest disadvantage is that it is noisy. So since the 1960s, it has been gradually replaced by hydraulic driven cutting machines.
What is a Manual Clicker Press ?
Mechanical clicker presses were once the industry standard, offering a reliable and efficient solution for cutting various materials. These machines utilize a mechanical system to generate cutting force, often through a flywheel and crank mechanism.
While mechanical presses offer certain advantages, such as simplicity and durability, they also have some limitations:
- Noise: Mechanical presses can be quite noisy due to the moving parts involved in the cutting process.
- Limited Cutting Force: The maximum cutting force is constrained by the mechanical design.
- Potential for Inconsistency: Over time, wear and tear can affect the precision and consistency of the cutting process.
As technology advanced, hydraulic clicker presses emerged as a superior alternative. These machines offer several advantages over their mechanical counterparts, including:
- Quieter Operation: Hydraulic systems are significantly quieter, making them more suitable for noise-sensitive environments.
- Precise Control: Hydraulic systems allow for precise control over cutting force and stroke length.
- Higher Cutting Force: Hydraulic presses can generate much higher cutting forces, enabling the processing of thicker and denser materials.
While mechanical clicker presses still have a place in certain applications, hydraulic presses have become the preferred choice for many industries due to their superior performance and efficiency.
Which is the Best ? Manual Clicker Press VS Hydraulic Clicker Press?
The choice between a hydraulic and a manual clicker press depends on your specific needs. Here’s a breakdown of their key differences:
Hydraulic Clicker Press:
- Advantages:
- Greater Cutting Force: Utilizes hydraulics to generate significantly more cutting power, enabling you to handle thicker and denser materials.
- Faster Operation: Offers faster cutting cycles, improving production efficiency.
- Reduced Labor: Requires less physical effort compared to manual operation.
- Greater Versatility: Works well with larger materials and allows for the use of complex cutting dies.
- Disadvantages:
- Higher Cost: Hydraulic presses are generally more expensive than manual ones.
- Maintenance Requirements: Requires regular maintenance of the hydraulic system.
- Hydraulic Oil: Needs refilling with hydraulic oil, adding an operational cost.
Manual Clicker Press:
- Advantages:
- Lower Cost: Significantly cheaper than hydraulic models.
- Simple Operation: Requires minimal training and maintenance.
- Ideal for Low Volume: Perfect for situations with low production needs.
- Less Bulky: Takes up less space compared to hydraulic presses.
- Disadvantages:
- Limited Cutting Force: Restricted force capability, limiting material thickness and die complexity.
- Slower Operation: Requires more manual effort and results in slower cutting cycles.
- Limited Versatility: May not be suitable for larger materials or intricate cutting dies.
Feature | Hydraulic Clicker Press | Manual Clicker Press |
---|---|---|
Cutting Force | Higher | Lower |
Operation Speed | Faster | Slower |
Labor Requirements | Less | More |
Versatility | Greater | Limited |
Initial Cost | Higher | Lower |
Maintenance | More complex | Less complex |
Noise Level | Quieter | Louder |
Power Source | Hydraulic power | Manual power |
Choosing the Right Clicker Press:
- Low Volume & Small Materials: Manual presses are a good option for small-scale operations, limited cutting needs, and materials manageable with less force.
- High Volume & Thick Materials: If you require high production volume, handle thicker or denser materials, or plan to use large and complex cutting dies, a hydraulic press is the better choice.
Ultimately, consider your budget, production volume, material types, and desired cutting speed to make the right decision for your needs.
What is the Difference between Swing Arm Clicker Press and Beam Press?
Swing Arm Clicker Press
- Design: Features a swinging arm or beam that moves left and right.
- Material Size: Best suited for smaller materials and dies.
- Operation: Typically manual feeding, requiring operator intervention for each cutting cycle.
- Applications: Ideal for small-scale production, hobbyists, and prototyping.
Full Beam Clicker Press
- Design: Equipped with a full-width beam that moves up and down.
- Material Size: Capable of handling larger materials and dies.
- Operation: Can be manual or automatic, with automatic feeding systems increasing productivity.
- Applications: Commonly used in industrial settings for high-volume production of various materials.
Feature | Swing Arm Clicker Press | Full Beam Clicker Press |
---|---|---|
Beam Design | Swinging arm | Full-width beam |
Material Size | Smaller materials and dies | Larger materials and dies |
Operation | Manual feeding | Manual or automatic feeding |
Production Volume | Suitable for small-scale production | Ideal for high-volume production |
Cost | Generally more affordable | Typically more expensive |
Applications | Hobbyists, small businesses, prototyping | Industrial settings, large-scale production |
Key Differences and Considerations:
- Material Size: Full beam presses are better suited for larger materials and dies due to their wider cutting area.
- Production Volume: For high-volume production, automatic feeding capabilities of full beam presses can significantly increase efficiency.
- Operator Skill and Fatigue: Manual feeding of swing arm presses can be physically demanding, especially for extended periods.
- Cost: Full beam presses, especially automatic models, tend to be more expensive than swing arm presses.
Choosing the Right Press:
When selecting a clicker press, consider the following factors:
- Material Size and Thickness: The size and thickness of the materials you’ll be cutting will determine the required cutting force and table size.
- Production Volume: If you have high-volume production needs, an automatic full beam press can significantly increase efficiency.
- Operator Skill and Budget: Manual swing arm presses are a good option for smaller operations and those with limited budgets.
- Future Needs: Consider your future production needs and potential growth to choose a press that can adapt to your evolving requirements.
Conclusion: Both are very good die-cutting machines. Swing arm is more suitable for small batch production and cutting small materials. The beam press is more suitable for mass production, and large parts and die.By carefully evaluating these factors, you can select the most suitable clicker press to meet your specific needs.
Why do You Need a Swing Arm Clicker Press ?
A swing arm clicker press is an essential tool for efficient and precise cutting of various materials, especially in industries like footwear, leather goods, textiles, and packaging.
Here’s why:
- Precision Cutting:
- Ensures consistent and accurate cuts, reducing material waste.
- Produces identical parts, maintaining product quality.
- Increased Efficiency:
- Significantly faster than manual cutting methods.
- Reduces labor costs and increases production output.
- Versatility:
- Can handle a wide range of materials, including leather, fabric, paper, and plastic.
- Can cut various shapes and sizes, depending on the die used.
- Safety:
- Reduces the risk of accidents and injuries associated with manual cutting.
- Reduced Material Waste:
- Precise cutting minimizes material waste, saving costs.
In essence, a swing arm clicker press is a valuable investment for businesses that need to produce high-quality, consistent products efficiently.
What are the Advantages of Swing Arm Clicker Press?
Swing arm clicker presses are versatile machines that offer numerous advantages for a variety of industries. Here’s a breakdown of their key benefits:
Precision and Consistency
- Accurate Cuts: Ensures precise cuts, minimizing material waste and maximizing product quality.
- Consistent Results: Maintains consistent cutting pressure, leading to uniform product quality.
Versatility
- Wide Material Compatibility: Handles a broad range of materials, including leather, fabric, rubber, and plastics.
- Diverse Applications: Suitable for various industries, such as footwear, apparel, automotive, and packaging.
Ease of Use
- User-Friendly Design: Intuitive controls and simple operation.
- Minimal Training Required: Operators can quickly learn to use the machine efficiently.
Space Efficiency
- Compact Footprint: Ideal for smaller workshops and production facilities.
Reduced Labor Costs and Improved Safety
- Automated Cutting: Reduces the need for manual labor, leading to cost savings.
- Enhanced Safety: Built-in safety features minimize the risk of accidents and injuries.
High Production Speed
- Rapid Cutting Cycles: Increases overall production efficiency.
Durability and Longevity
- Robust Construction: Ensures long-lasting performance.
- Minimal Maintenance: Requires minimal upkeep.
Customization Options
- Tailored Solutions: Can be customized to meet specific industry needs and production requirements.
By combining these advantages, swing arm clicker presses offer a powerful and efficient solution for businesses across various industries.
What are the disadvantages of Swing Arm Clicker Press?
While swing arm clicker presses offer numerous advantages, they also come with certain limitations:
Material Thickness and Complexity Limitations
- Limited Material Thickness: These machines are generally designed for cutting materials within a specific thickness range. Thicker or denser materials may require more powerful machinery.
- Cutting Complexity: While suitable for many shapes, swing arm presses may struggle with highly complex or intricate designs.
Operational Considerations
- Maintenance Requirements: Regular maintenance, including lubrication and part replacement, is essential to ensure optimal performance.
- Operator Skill: Skilled operators are needed to set up the machine correctly and achieve precise cuts.
- Noise Levels: The mechanical operations of these machines can generate significant noise, requiring noise reduction measures in the workplace.
Cost Implications
- Initial Investment: The upfront cost of purchasing a swing arm clicker press can be substantial.
- Die Costs: High-quality cutting dies can be expensive, especially for intricate designs.
Space Requirements
- Physical Footprint: These machines can be relatively large, requiring adequate space in production facilities.
By understanding these limitations, businesses can make informed decisions about the suitability of swing arm clicker presses for their specific production needs.
What Power Configurations are for Swing Arm Clicker Presses?
Gerson Swing arm clicker presses are available in various power configurations to accommodate different electrical systems and regional standards. Common power options include:
Single-Phase Power:
- 110V
- 220V
- 240V
Three-Phase Power:
- 220V
- 380V
- 415V
- 440V
It’s important to consult Gerson to determine the specific power requirements for a particular model. They can provide tailored solutions based on your location’s electrical infrastructure.
Gerson offers a wide range of power configurations to meet global needs. We can provide machines that are compatible with various voltage and frequency standards, ensuring optimal performance in different regions.
Can I Use Different Dies in a Single Swing Arm Clicker Press ?
Yes, you can use different dies in a single swing arm clicker press.
Our beauty of a swing arm clicker press lies in its versatility. By simply switching out the cutting die, you can change the shape and size of the cut pieces. This flexibility allows for a wide range of applications and products to be produced using the same machine.
To change the die, you typically need to Adjust the Press: Depending on the die’s height and the desired cutting depth, you may need to adjust the press’s settings. Gerson clicker presses are capable of handling different heights of cutting dies, particularly through their GR Series with automatic stroke adjustments and other models that facilitate easy transitions between various die sizes. This means that operators can use dies of varying thicknesses without needing to recalibrate or adjust the machine settings each time a different die is used.
Gerson also have the three key model which supports the use of different sized dies by providing three distinct cutting pressures. This feature enables users to work with dies of varying surface areas without having to make repetitive adjustments, thereby enhancing productivity and efficiency.
So ,You can use different dies produce a variety of products using a single swing arm clicker press.
How do You Adjust the Stroke Depth on a Swing Arm Clicker Press?
To adjust the stroke depth on a swing arm clicker press, you typically need to locate and adjust the daylight adjustment wheel. This wheel controls the vertical travel of the cutting head, allowing you to set the desired depth of the cut.
By turning the wheel, you can increase or decrease the distance between the cutting head and the cutting table. This adjustment is crucial for ensuring accurate cuts and preventing damage to the cutting die or material.
Note: The specific method for adjusting stroke depth may vary slightly depending on the make and model of the press. Always refer to the our manual for precise instructions.
If you have any further questions or need more specific guidance, please consult the Gerson swing arm clicker press’ manual or contact a Gerson qualified technician.
How Do You Choose a Swing Arm Clicker Press?
When considering a swing arm clicker press, it’s important to assess your specific needs and budget. Here’s a step-by-step guide to help you make an informed decision:
1. Define Your Needs:
- Production Volume: Determine the volume of production required. For small-scale operations, a manual or semi-automatic press might suffice. For large-scale production, a fully automatic press may be more suitable.
- Material Thickness and Size: Consider the thickness and size of the materials you’ll be cutting. This will influence the required cutting force and table size.
- Cutting Complexity: Assess the complexity of the shapes and patterns you need to cut. More intricate designs may require a more advanced press with precise control.
- Budget: Establish a budget for the purchase and ongoing maintenance of the press.
2. Choose the Right Type of Press:
- Mechanical vs. Hydraulic: Mechanical presses are simpler and more affordable, but hydraulic presses offer greater power and precision.
- Swing Arm vs. Full Beam: Swing arm presses are suitable for smaller materials and manual operation. Full beam presses are better suited for larger materials and can be automated for higher production volumes.
3. Consider the Following Factors:
- Cutting Force: Ensure the press has sufficient cutting force to handle your materials.
- Table Size: Choose a press with a table size that accommodates your largest materials.
- Power Source: Consider the availability of power sources (single-phase or three-phase) and voltage requirements.
- Safety Features: Look for safety features like emergency stop buttons and guards to protect operators.
- Maintenance Requirements: Evaluate the ease of maintenance and the availability of spare parts.
4. Consult with Experts:
- Seek Expert Advice: Consult with experienced professionals or manufacturers to get personalized recommendations.Gerson is rich experience manufacturer that will help you to choose the right press .You could contact us freely.
- Provide Detailed Information: Share your specific requirements, including material types, dimensions, and production volume.
By carefully considering these factors, you can select the most appropriate swing arm clicker press for your specific needs. Gerson is ready to assist you in finding the perfect solution. Please feel free to contact us with your requirements, and our experts will provide tailored recommendations.
Which Swing Arm Clicker Press do Gerson Have in Stock for Sale ?
Gerson typically stocks popular models of swing arm clicker presses, such as the GR, GRA and GSB series, to ensure prompt delivery. However, for specific customizations or less common models, production time may be required.
To confirm availability and delivery times for your specific needs, please contact us directly. Our sales team will be happy to assist you and provide accurate information.
What is the Price of Gerson Swing Arm Clicker Press ?
At Gerson, we’re dedicated to providing cost-effective, high-quality swing arm clicker presses. Our competitive pricing is made possible by:
- Efficient Production: Our streamlined production processes and experienced workforce minimize costs, allowing us to offer competitive prices.
- Economies of Scale: As a leading manufacturer, we benefit from economies of scale, which helps us reduce production costs.
- Strategic Sourcing: We source high-quality components at competitive prices, further contributing to our cost-effectiveness.
- Long-Standing Expertise: With years of experience in the industry, we have honed our manufacturing techniques to maximize efficiency and minimize costs.
By combining these factors, we’re able to offer our customers exceptional value without compromising on quality.
How Does Maintain a Swing Arm Clicker Press ?
Proper maintenance is essential to ensure the longevity and optimal performance of your swing arm clicker press. Here are some key maintenance tips:
Regular Maintenance:
- Hydraulic System:
- Fluid Level: Regularly check and maintain the hydraulic fluid level.
- Fluid Quality: Ensure the hydraulic fluid is clean and free of contaminants.
- Filter Replacement: Replace filters as recommended by the manufacturer to prevent system damage.
- Seal Inspection: Inspect seals and fittings for leaks and replace them as needed.
- Mechanical Components:
- Lubrication: Lubricate moving parts, such as bearings and linkages, according to the manufacturer’s recommendations.
- Cleaning: Keep the machine clean and free of debris to prevent damage and ensure smooth operation.
- Belt and Pulley Inspection: Check belts and pulleys for wear, alignment, and tension.
- Electrical Components:
- Wiring: Inspect wiring for damage or loose connections.
- Control Panel: Clean and inspect the control panel and its components.
Safety Considerations:
- Regular Inspections: Conduct regular safety inspections to identify and address potential hazards.
- Operator Training: Ensure operators are trained on proper machine operation and safety procedures.
- Emergency Stops: Test emergency stop buttons and safety interlocks to ensure they function correctly.
By following these maintenance guidelines, you can prolong the life of your swing arm clicker press, improve its performance, and reduce downtime.
Remember to consult our Gerson specific user manual for detailed maintenance instructions.
Conclusion
The swing arm clicker press, with its classic design and practical functionality, has proven its worth for over a century. Its simple, swinging arm mechanism remains a workhorse in diverse industries, from small workshops to large factories, efficiently cutting a variety of materials. The ease of use and quick die changes make it highly adaptable to different production requirements. Even with advancements in technology and automation, the swing arm clicker press remains a popular choice, especially for small businesses, hobbyists, and situations prioritizing flexibility and affordability. Its durable build and straightforward maintenance ensure a long lifespan, making it a reliable and economical investment. For clean, precise cuts and efficient production, whether working with leather, fabric, or other materials, the swing arm clicker press continues to be a valuable and relevant tool.