Foam and sponge die cutting machines are specialized industrial equipment designed to accurately and efficiently cut foam and sponge materials into a wide range of shapes and sizes. These machines utilize precision cutting techniques, such as steel rule die cutting, to produce intricate components used in various industries.. These machines achieve this by employing sharp cutting tools that precisely slice through foam materials.
Types of Foam Sponge Die Cutting Machine:
The right machine for you depends on your specific needs. Here’s a breakdown of the main options:
1. Manual Feed Die-Cutting Machines:
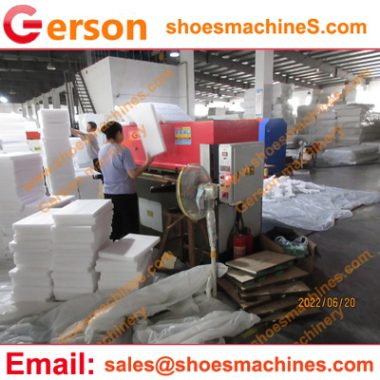
A manual feed foam sheet die cutting machine is a mechanical device used to cut precise shapes and patterns from foam sheets. It uses a steel rule die, which is a hardened steel plate with sharp cutting edges, to punch out the desired shape. The operator manually positions the foam sheet on the machine’s bed and then activates the cutting mechanism.
Advantages of Manual Feed Foam Sponge Die Cutting Machines:
- Low cost: Manual machines are generally more affordable than their automatic counterparts.
- Easy to operate: They require minimal training and are simple to use.
- Versatile: They can handle a wide range of foam materials and thicknesses.
- Low maintenance: Manual machines have fewer moving parts, reducing the need for regular maintenance.
- Adjustable Cutting Force: The cutting force can be adjusted to accommodate different material thicknesses and die designs.
- Safety Features: Safety guards and emergency stop buttons are included to protect the operator.
Disadvantages of Manual Feed Foam Sponge Die Cutting Machines:
- Labor-intensive: The operator must manually feed each sheet of foam, which can be time-consuming and repetitive.
- Lower production speed: Compared to automatic machines, manual machines have a slower production rate.
2.Automatic Feed Die-Cutting Machines:
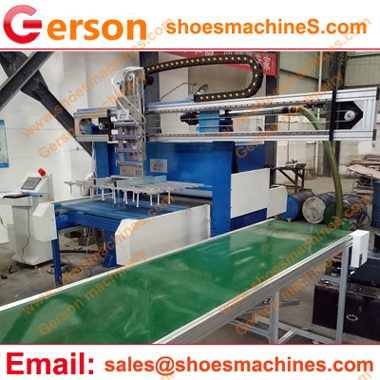
Automatic feed die cutting machine offer a balance between efficiency and cost-effectiveness for foam and sponge cutting. These machines automate the material feeding process, significantly increasing production speed and reducing operator fatigue.For more information ,you could check on beam press page.
Here are some key features and benefits of semi-automatic die-cutting machines with automatic feed:
Features:
- Automatic Feeding System: The machine is equipped with a conveyor or roller system that automatically feeds the foam or sponge material into the cutting area. Offers a balance, combining manual loading with automated cutting for increased efficiency.
- Fully autoamtion option : These machines can automatically feed, cut, pick-up and stack foam , minimizing manual intervention. (Ideal for high-volume operations) Utilize computer numerical control (CNC) technology for unmatched precision and complex designs.Perfect for intricate shapes and small-batch production runs.
- Automatic Feeding of Both Sides of the Sheet:
- Purpose: Ensures continuous and efficient feeding of foam sheets, reducing downtime.
- Mechanism: Often involves a conveyor system with rollers or belts that can flip and feed sheets from both sides.
- Winding Device for Coils:
- Purpose: Stores excess foam material in a coiled format, reducing waste and optimizing material usage.
- Mechanism: A winding mechanism with rollers and tension control to wind the coiled material.
- Material Feed Roller:
- Purpose: Controls the precise feeding of foam sheets into the cutting area.
- Mechanism: Roller system with adjustable speed and pressure to ensure accurate feeding.
- Foam Sheet Stacking Device:
- Purpose: Organizes cut foam sheets into stacks for easy handling and transport.
- Mechanism: A robotic arm or pneumatic system to pick and place cut sheets onto a stacking pallet.
- Automatic Finished Products Pick-up Device:
- Purpose: Removes finished cut parts from the cutting area, increasing efficiency.
- Mechanism: Robotic arm or vacuum system to pick up and place finished parts in a designated area.
- Waste Materials Re-winding Device:
- Purpose: Collects and rewinds waste foam material, reducing waste and maximizing material utilization.
- Mechanism: Similar to the winding device for coils, but designed for smaller pieces of waste material.
- Clamping Beam:
- Purpose: Holds the foam sheet securely in place during the cutting process.
- Mechanism: A pneumatic or hydraulic system to apply clamping force to the sheet.
- Inboard Pneumatic Pinch Roll Feeding System:
- Purpose: Provides precise control over the feeding of the foam sheet into the cutting area.
- Mechanism: Pneumatic cylinders control the pressure of the pinch rollers to ensure accurate feeding.
Additional Considerations for Automation:
- Vision Systems: To detect the position and orientation of foam sheets for accurate feeding and cutting.
- Sensor Systems: To monitor machine performance and detect potential issues.
- PLC Control: To automate the sequence of operations and control the various components.
- Human-Machine Interface (HMI): To provide a user-friendly interface for monitoring and controlling the machine.
By incorporating these components and technologies, you can create a highly automated foam cutting machine that significantly improves productivity, reduces labor costs, and minimizes waste.
Benefits:
- Increased Productivity: Automatic feeding eliminates the need for manual material handling, leading to higher production rates.
- Reduced Labor Costs: Fewer operators are required to run the machine, lowering labor costs.
- Improved Accuracy: Consistent feeding ensures accurate and precise cuts.
- Reduced Material Waste: Efficient cutting minimizes material waste.
- Versatility: Suitable for a wide range of foam and sponge materials and die designs.
3.Custom-Built Machines:
Gerson Machinery is a leading provider of high-quality foam and sponge cutting machines, offering a wide range of solutions to meet various production needs.Tailor-made solutions for unique cutting challenges.Optimized for specific foam and sponge materials and thicknesses.
The specific specifications for a custom-built foam die-cutting machine will vary depending on your exact needs. However, here are some common factors to consider:
Size and Table Size:
- Machine Size: This will depend on the size of the foam sheets you plan to cut and the complexity of the dies. Larger machines can accommodate larger sheets and more complex cutting operations.
- Table Size: The table size should be sufficient to accommodate the largest foam sheet you’ll be cutting, along with the die and any necessary tooling.
Cutting Force:
- The required cutting force will depend on the thickness and density of the foam material, as well as the complexity of the die. A higher cutting force is generally needed for thicker and denser materials.
Feed Type for sheet or roll foam and sponge :
- Manual Feed: The operator manually positions the foam sheet on the cutting table. Suitable for low-volume production or simple shapes.
- Semi-Automatic Feed: A conveyor system automatically feeds the foam sheet into the cutting area. Increases productivity and reduces operator fatigue.
- Fully Automatic Feed: A robotic arm or similar system automatically feeds, positions, and removes the cut parts. Ideal for high-volume production and complex cutting operations.
Common Foam Types for Die Cutting
Foam Type | Key Characteristics | Common Applications | Examples |
---|---|---|---|
Polyurethane Foam | Soft, flexible, good insulation | Packaging, cushioning, furniture, automotive | Furniture cushions, packaging inserts, soundproofing materials |
Polyethylene Foam | Durable, chemically resistant, good insulation | Packaging, insulation, gaskets, seals | Packaging for electronics, insulation for pipes, gaskets for appliances |
Ethylene Vinyl Acetate (EVA) Foam) | Flexible, impact resistant, good thermal insulation | Sports equipment, footwear, packaging | Shoe insoles, yoga mats, packaging inserts |
Neoprene Foam | Oil, grease, and chemical resistant | Gaskets, seals, protective padding | Gaskets for appliances, seals for windows and doors, protective padding for electronics |
Rubber Foam | Elastic, shock absorbent, durable | Gaskets, seals, cushioning | Gaskets for automotive parts, seals for industrial equipment, cushioning for packaging |
Polystyrene Foam | Lightweight, good insulation | Packaging, insulation, crafts | Packaging peanuts, insulation for buildings, craft foam sheets |
Silicone Foam | High-temperature resistant, flexible | Gaskets, seals, medical devices | Gaskets for ovens, seals for medical equipment |
Why are they important?
- Precision Cutting: Accurate cuts ensure a snug fit for your products, offering superior protection during transport and storage.
- Material Versatility: From EPE and EVA to polyurethane, these machines handle a wide range of foam types.
- Customization for Every Need: Die-cutting allows for creating inserts of any shape, size, and thickness, perfectly tailored to your specific product requirements.
- Efficiency Boost: Automated machines significantly speed up production and reduce labor costs compared to manual cutting.
Choosing the Right Machine:
Here are some key factors to consider when selecting your foam insert die-cutting machine:
- Production Volume: Low volume? A manual or semi-automatic option might suffice. High volume? Fully automatic or CNC machines are better choices.
- Complexity of Cuts: For simple shapes, basic machines work well. Intricate designs necessitate a CNC machine for optimal results.
- Foam Material: Different foams may require specific cutting tools and machine configurations.
- Budget: Consider initial investment, operating costs, and maintenance requirements.
By carefully evaluating these factors, you can select the machine that perfectly aligns with your production needs and budget.
Gerson Machinery’s commitment to quality, innovation, and customer satisfaction has made them a trusted partner for businesses in various industries more than 38+ years. Whether you need a simple manual machine or a fully automated production line, Gerson can provide the right solution to meet your foam and sponge cutting needs.