Custom Cutting Die
Manufacturer&Supplier
38+ Years
High Quality Same as in Europe
Experienced Skilled Engineers
Fast Delivery & Full Support
Cheap Affordable Price
Leading Custom Cutting Die Manufacturer
Gerson have been a leading cutting die company.Our dedicated engineers and continuous investment in R&D drive us to manufactured custom cutting-edge die cutting solutions.
We manufactured a wide range of custom dies, including steel rule die, pre-sharp die, forging die,machined die,rotary die ,match-metal die ,scrap removal cutting die,hole punch, creasing, thermal, embossing, and R&D sample tooling, providing versatile options to meet your specific needs. Explore our custom die cutting services below to discover how we can enhance your products.
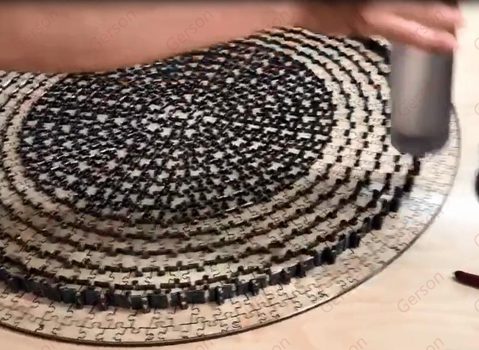
Custom Cutting die Fabrication
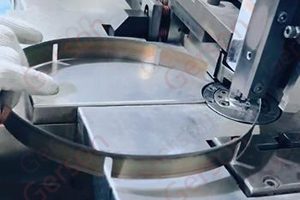
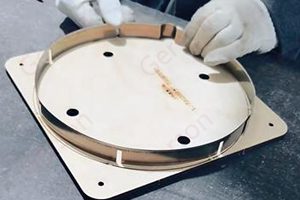
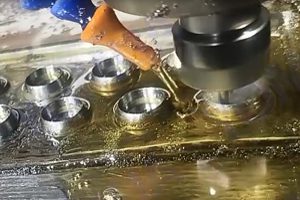
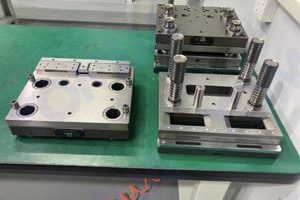
Gerson Custom Cutting die
Steel Rule Cutting Die
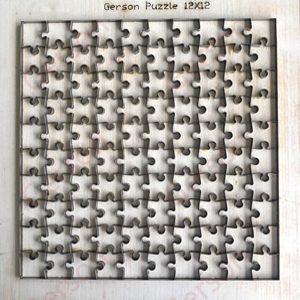
It consists of a sharp steel rule that is bent into a specific shape and mounted on a die board. Steel rule cutting dies are known for their versatility, accuracy, and cost-effectiveness, making them a popular choice for both short and long production runs
Pre-Hard Pre-Sharp Dies
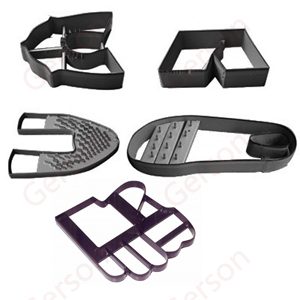
The cutting tools made with pre-hardened and sharpened steel, offering durability and precision for various cutting applications. It is eliminating the need for initial sharpening. This saves time and ensures consistent, clean cuts from the first use.
Machined Die
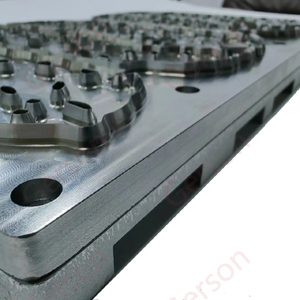
A machined die is a cutting or forming tool precisely crafted using machining processes. These dies are from durable materials like tool steel offer high accuracy and are often used for complex shapes in manufacturing processes such as stamping, forging, and die casting.
Forged Die
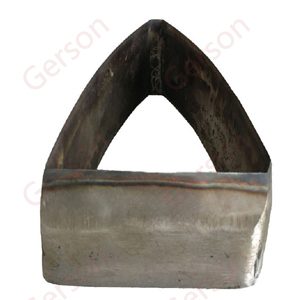
A forged die is a tool used in forging, where metal is shaped by compressive forces. These dies are typically made from durable materials like steel and are used to create complex shapes with high strength and durability. Forged dies are essential in many industries.
Rotary Die
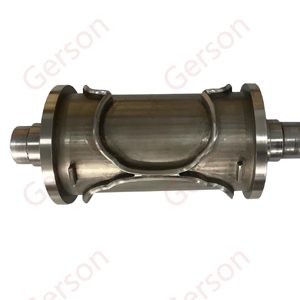
Rotary dies are cylindrical cutting tools used in rotary die cutting machines. They rotate to cut materials like paper, cardboard, and plastics into desired shapes with high speed and precision, ideal for large production runs.
Match-metal Die
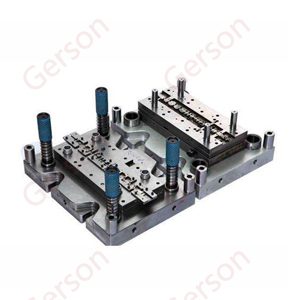
Match-metal dies consist of two precisely aligned dies, a male and a female, that work together to cut or form materials. The close fit between the dies ensures clean, accurate cuts and intricate shapes, often used for blanking, piercing, and embossing in various industries.
Scrap Removal Cutting Die
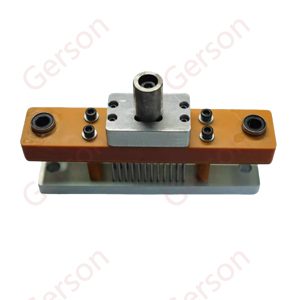
A scrap removal cutting die is designed to not only cut a desired shape but also efficiently remove the excess material (scrap) in a single operation. This streamlines the production process and reduces waste, making it ideal for high-volume manufacturing.
Punch Press Cutting Die
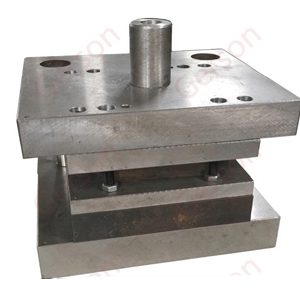
A punch press cutting die is a tool used in a punch press machine to cut, form, or pierce materials. These dies, often made of hardened steel, work in conjunction with the punch press to create specific shapes in a variety of materials quickly and efficiently.
Custom Cutting Die Application
Material and products in Application
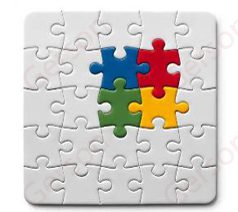
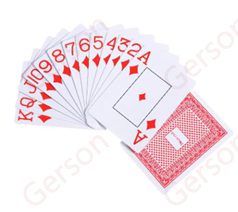
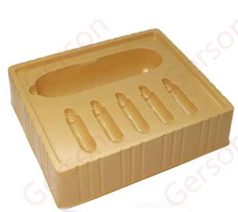
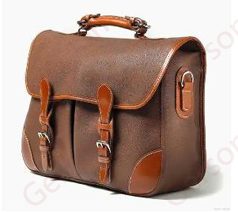
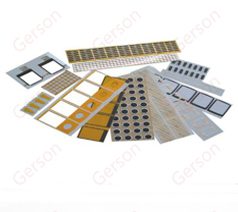
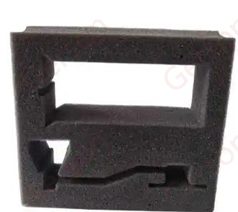
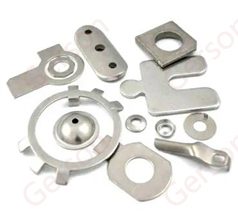
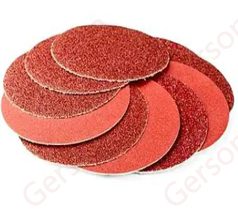
Material | Common Products Made with Custom Cutting Die mold tools |
---|---|
Paper | Stationery (cards, envelopes, letterheads), Crafts (scrapbook embellishments, paper flowers), Packaging (small boxes, tags, labels), Printing (bookmarks, brochures, business cards) |
Cardboard | Packaging (shipping boxes, retail packaging), Displays (signage, product displays), Crafts (3D models, masks) |
Paperboard | Packaging (folding cartons), Printing (postcards, tickets), Crafts (book covers, presentation folders) |
Corrugated Board | Packaging (shipping boxes, protective packaging), Displays (retail displays, signage), Other (furniture components) |
Plastic | Packaging (clamshells, blister packs), Signage (indoor/outdoor signs), Promotional Items (keychains, magnets), Industrial (gaskets, seals) |
Foam | Packaging (protective cushioning), Crafts (foam shapes, letters), Toys (foam puzzles), Other (soundproofing, insulation) |
Rubber | Gaskets (seals, washers), Automotive (floor mats, weather stripping), Industrial (vibration dampeners), Other (mouse pads, stamps) |
Fabric | Clothing (appliqués, patches), Crafts (fabric shapes, quilting pieces), Home Decor (coasters, placemats), Other (bags, wallets) |
Leather | Accessories (belts, wallets, handbags), Clothing (patches, labels), Other (bookmarks, coasters) |
Metal | Industrial (washers, shims, gaskets), Automotive (trim pieces, emblems), Electronics (shielding, connectors), Other (jewelry components) |
Film | Packaging (labels, overlays), Electronics (screen protectors), Printing (decals, stickers), Other (medical applications) |
Foil | Packaging (food packaging, seals), Insulation (thermal insulation), Crafts (decorative accents), Other (electronics) |
Related Products with Custom Cutting Die mold
A roller die cutter press uses a rolling mechanism to apply pressure to a die, cutting materials like paper, fabric, or leather. It’s ideal for efficient, consistent cuts in crafting or light industrial settings.
A beam press is a powerful die-cutting machine that uses a horizontal beam to apply pressure across a large cutting area. It’s ideal for high-volume production and cutting thick or tough materials.
Hydraulic Press
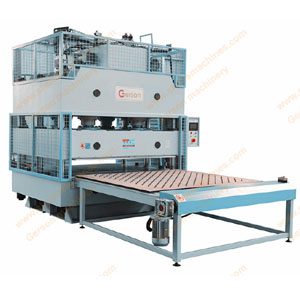
A hydraulic press is a powerful die-cutting machine that utilizes hydraulic fluid to generate immense pressure. with a die, allowing it to cut through thick, dense, or multiple layers of materials
Custom Cutting Die Mold tools : Definitive Buying Guide(keep updating: Updated on Feb. 15th, 2025.)
Custom Cutting die mold tools: Buying Guide
What is a Cutitng Die?
A cutting die is a specialized tool, or mold, used in the die-cutting manufacturing process to create specific shapes from various materials. It’s essentially a sharp-edged metal shape, similar to a cookie cutter, that, when pressed onto a material, cuts out the desired design. These tools are critical for efficient and precise production in a wide range of industries.
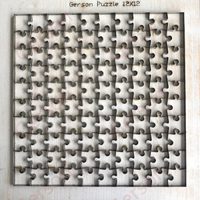
Conclusion:
- Essential Tools: cutting dies are essential tools in modern manufacturing, enabling the efficient and precise creation of countless products from a diverse range of materials.
- Material: From packaging and textiles to automotive parts and electronics, these specialized tools, or molds, play a crucial role in shaping the world around us.
- Die-cutting Process: utilizing these sharp-edged metal forms, ensures consistent quality and high-volume production, making cutting dies indispensable for a multitude of industries.
In summary, a cutting die is an essential tool in both crafting and manufacturing that allows for efficient and accurate production of shaped materials.
Why Do You Need a Cutting Die tool?
Cutting die tools are indispensable for crafters, particularly those involved in card making, scrapbooking, and paper crafts. These tools enable the creation of precise, consistent shapes from various materials, significantly improving project quality and efficiency.
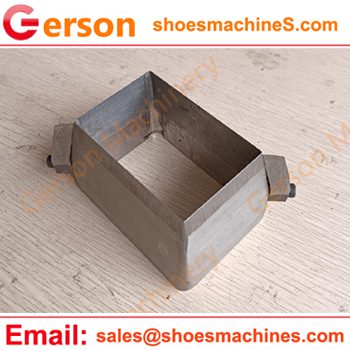
Efficiency in Crafting: One of the biggest advantages of a cutting die tool is the efficiency it brings to crafting. Traditional cutting methods with scissors or craft knives are time-consuming and often lead to uneven edges and inconsistent sizes. A cutting die tool allows for the rapid production of multiple identical shapes with accuracy. This is especially valuable when creating items like invitations or decorations requiring numerous uniform pieces.
Professional Quality Results: Cutting die tools deliver professional-quality results. The precision of the dies ensures clean cuts, enhancing the overall look of crafted items. This is crucial for projects where aesthetics are paramount, such as handmade cards or custom gifts. The uniformity achieved across multiple pieces contributes significantly to the polished finish.
Versatility in Materials: Cutting die tools are incredibly versatile, working with a wide range of materials beyond paper, including cardstock, fabric, thin plastic, and even certain metals. This versatility expands creative possibilities, allowing crafters to explore different textures and finishes in their projects.
Types of Cutting Die Tools: Two main types of cutting die tools exist: manual and digital. Manual machines use a crank mechanism to press dies onto materials, while digital machines employ electronic blades controlled by software. Each type offers unique benefits. Manual machines are generally more affordable and straightforward, while digital machines provide greater design flexibility and automation.
Cost-Effectiveness: Investing in a cutting die tool can be cost-effective in the long run. While there’s an initial investment for the machine and dies, the ability to create custom designs without purchasing pre-made items saves money. Many crafters also find they can sell their handmade creations for profit, further offsetting the initial costs.
Conclusion: For anyone serious about crafting, a cutting die tool is essential. Its efficiency, ability to produce professional-quality results, versatility with various materials, options for manual and digital operation, and long-term cost-effectiveness make it an invaluable asset. These combined factors enhance both the crafting experience and the quality of the finished products.
Do I Need a Die Cutting Machine for cutting die tool?
The question of whether you need a die-cutting machine for your die tools depends largely on the specifics of your crafting or production needs. While some simple projects with thin materials can be managed without a machine, for most applications, a die-cutting machine is a worthwhile, and often essential, investment.
Manual Cutting: A Limited Solution
For thin materials like paper, cardstock, or lightweight fabric, manual cutting with a die, hand roller, or mallet is possible. This involves placing the die on the material and applying pressure to cut through it. This method is inexpensive and portable, making it suitable for small, occasional projects. However, it requires physical effort, can be slow, and struggles with thicker or tougher materials. Achieving consistent, even pressure is also challenging, leading to potentially uneven or imprecise cuts.
The Advantages of a Die-Cutting Machine
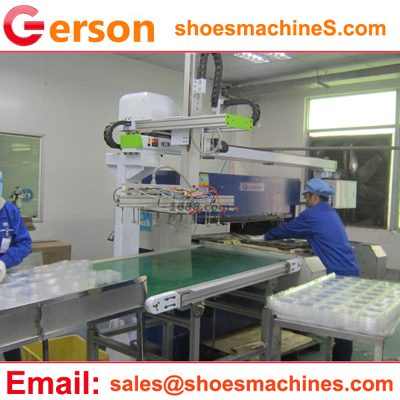
Die-cutting machines address the limitations of manual cutting, offering significant benefits:
- Consistent Cuts: Machines apply even pressure across the die, ensuring clean, uniform cuts every time. This is crucial for professional-looking results and efficient production.
- Material Versatility: Die-cutting machines can handle a wider range of materials, including thicker materials like leather, chipboard, multiple layers of fabric, and heavier cardstock. This versatility opens up a world of creative possibilities.
- Efficiency and Speed: For larger projects or when producing multiple identical pieces, die-cutting machines are significantly faster and more efficient than manual cutting. This is especially true for repetitive cuts.
- Precision and Intricate Designs: Machines allow for greater precision, especially when working with intricate die designs. They ensure clean cuts even with complex shapes.
Gerson’s Range of Machines:
Gerson offers a variety of die-cutting machines to suit different needs and budgets. From manual tabletop machines for smaller projects to large-volume CNC automatic machines for industrial production, there’s likely a Gerson machine that fits your requirements.
Choosing the Right Machine:
When selecting a die-cutting machine, consider factors such as:
- Material Compatibility: What types of materials will you be cutting?
- Volume: How many pieces do you need to produce?
- Budget: How much are you willing to invest in a machine?
- Space: How much space do you have available for the machine?
By carefully considering these factors, you can choose the right die-cutting machine to maximize your productivity and achieve the desired results.
When a Machine Might Not Be Necessary
If you only occasionally craft with thin materials and simple shapes, manual methods might suffice. Additionally, some specialized dies are designed for use with alternative tools like die punches or hammers. However, these methods are usually less precise and more limited in material compatibility.
Conclusion: The Investment in Efficiency and Quality
While manual cutting is an option for very basic projects, a die-cutting machine is a valuable investment for most crafters and essential for anyone working with thicker materials, intricate designs, or needing to produce items in larger quantities. The improved precision, consistency, and efficiency offered by these machines significantly enhance both the quality of finished products and the overall crafting experience. Consider your project needs, material choices, and budget to determine the best type of machine for you.
What Kinds of Cutting Die that Gerson can manufacture?
Steel Rule Die: These are the most common and cost-effective type. A sharp steel rule is bent into the desired shape and mounted in a wooden or composite base. They are suitable for cutting softer materials like paper, cardboard, fabric, and thin plastics. They are good for shorter runs and simpler designs.
Pre-Sharpen Die: These are similar to steel rule dies but use a pre-sharpened steel rule for even cleaner cuts and longer die life. They are a step up in quality from standard steel rule dies.
Forged Die: Forged dies are made from a single piece of steel that is shaped through a forging process. This creates a very durable die that can withstand high pressures and is ideal for cutting thicker or tougher materials like leather, rubber, and some plastics. They are more expensive than steel rule dies but offer superior durability.
Machined Die: Machined dies are made by precisely machining a block of steel. They offer the highest level of accuracy and are used for intricate designs and tight tolerances. They are also very durable and suitable for long production runs and thicker materials. These are among the most expensive die types.
Match Metal Die: Match metal dies consist of two parts: a male die (punch) and a female die (die cavity). The punch and cavity precisely match each other, allowing for very clean and accurate cuts, especially in materials like thin metal or when creating embossed designs. They are often used in combination with a press.
Rotary Die: Rotary dies are cylindrical and are used in rotary die-cutting machines. They are designed for high-speed, continuous cutting of materials in web form. They are common in printing and packaging applications for producing labels, boxes, and other products at high volumes.
Scrap Removal Cutting Die: These specialized dies incorporate features that automatically remove the scrap material after the cutting process. This increases efficiency, especially in high-volume production, by eliminating the need for manual scrap removal.
Punch Press Cutting Die: These dies are designed for use in punch presses. They are typically used for cutting or stamping operations in sheet metal or other relatively thin, flat materials. They can be single dies for simple shapes or progressive dies for more complex, multi-stage operations.
- Embossing dies:These dies are specialized tools used to create raised designs or textures on materials like paper, cardstock, metal, or fabric. Unlike cutting dies that slice through the material, embossing dies press into the material, creating a three-dimensional effect.
What's The Difference Between Cutting Die and Die Mold ?
While the terms “cutting die” and “die mold” are sometimes used interchangeably, there’s a key distinction between them, particularly in manufacturing contexts:
Cutting Die:
- Function: Primarily used for cutting materials. Think of it like a specialized cookie cutter. It has a sharp edge designed to slice through materials like paper, fabric, leather, or metal.
- Process: Involves applying pressure to the die to shear or cut the material.
- Materials: Works with solid materials in sheet or web form.
- Examples: Steel rule dies, forged dies, match metal dies. Used in industries like packaging, textiles, and printing.
Die Mold:
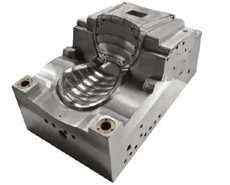
- Function: Used for shaping materials, often in a molten or pliable state. It forms a cavity into which the material is placed.
- Process: Involves filling the mold with a liquid or semi-fluid material (plastic, metal, etc.) which then solidifies to take the shape of the mold.
- Materials: Works with materials that can be melted or softened.
- Examples: Molds for injection molding, die casting. Used in industries like plastics manufacturing, metal casting.
Here’s a simple analogy:
- Cutting die: Like a cookie cutter, it cuts out a shape from dough (material).
- Die mold: Like a cake pan, it provides the shape for the cake batter (material) to solidify into.
Key Differences Summarized:
Feature | Cutting Die | Die Mold |
---|---|---|
Primary Function | Cutting | Shaping |
Material State | Solid (sheets, webs) | Liquid, semi-fluid |
Process | Shearing, cutting | Filling, solidification |
Important Note: In some contexts, particularly in metalworking, the term “die” can be used more broadly to encompass both cutting dies and die molds. However, it’s essential to understand the specific process being referred to when encountering these terms.
What are the Advantages of Using Custom Cutting Dies Over Traditional Methods
Custom cutting dies offer significant advantages over traditional cutting methods, making them a preferred choice for many industries. Here’s a detailed look at these benefits:
1. Precision and Accuracy: Custom dies excel in precision. They are engineered to cut materials into specific shapes and sizes with extreme accuracy, far surpassing the capabilities of traditional methods like manual cutting or even laser cutting, which can suffer from uneven edges and inaccuracies. This level of precision is crucial for industries requiring high-quality components with tight tolerances, such as electronics, medical devices, and aerospace.
2. Reduced Material Waste: A key advantage of custom dies is their ability to minimize material waste. Traditional cutting often leaves excess material due to imprecise cuts. Custom dies, however, are designed to maximize material utilization. By ensuring cuts are made precisely where needed, they significantly reduce scrap and optimize raw material usage, leading to cost savings and environmental benefits.
3. Increased Production Speed and Efficiency: Custom dies boost production speed and efficiency. Designed specifically for a particular shape or size, they enable manufacturers to produce parts quickly and consistently without constant adjustments or rework. This streamlined process leads to higher throughput, especially valuable in high-volume production environments where time is of the essence.
4. Improved Quality Control: Custom dies enhance quality control. Their precise design ensures each cut meets exact specifications, resulting in consistent output across all produced items. This consistency minimizes variability in production, reduces defects and errors, and ultimately saves money through lower scrap rates and less rework.
5. Versatility Across Materials: Custom dies can be crafted from various materials like steel, carbide, or rubber, enabling them to cut a wide range of substrates, including paper, plastic, metal, fabric, leather, foam, and rubber. This versatility makes them adaptable to diverse applications across multiple industries, allowing manufacturers to tailor their processes to specific project requirements.
6. Cost-Effectiveness in High-Volume Production: While creating custom dies involves an initial investment, they become highly cost-effective in high-volume production. The combination of reduced waste, increased speed, improved quality control, and material versatility leads to significantly lower operating costs over time compared to traditional cutting methods.
In summary: The advantages of custom cutting dies are numerous and compelling. They provide superior precision and accuracy, minimize material waste, increase production speed and efficiency, improve quality control, offer material versatility, and deliver cost-effectiveness in high-volume scenarios. These factors make custom dies a valuable asset for businesses seeking to optimize their manufacturing processes and produce high-quality products.
Do Gerson Accept One Custom Cutting Die ?
Gerson have NO minimum order quantities (MOQs) for custom dies.So Gerson accept an order for just one custom cutting die.
- Small-scale production: Gerson cater to smaller businesses or individual crafters who need only a single die for a specific project.
- Prototyping: Gerson could be open to creating a single die for prototyping purposes before moving on to larger production runs.
- Specialized requests: For unique or complex designs, Gerson is willing to create a single die.
How to inquire about a single custom die:
- Contact us: Reach out to our sales or customer service department through email or any online quote form.
- Explain your needs clearly:
- Describe the material you’ll be cutting.
- Provide a detailed design or drawing of the die you need.
- Specify the size and any other relevant details.
- Emphasize that you’re interested in a single custom die.
Gerson will reply to you in 12 hours.
How Long Does It Typically Take to Produce a Custom Cutting Die?
The time it takes to produce a custom cutting die can vary significantly depending on several factors. Here’s a breakdown of the typical timeline and the elements that influence it:
Factors Affecting Production Time:
- Die Complexity: Intricate designs with fine details will naturally take longer to manufacture than simple shapes.
- Die Type: Different die types have varying manufacturing processes. Steel rule dies are generally faster to produce than forged or machined dies.
- Material: The type of steel used for the die can impact production time.
- Size: Larger dies may require more time to fabricate than smaller ones.
- Quantity: If you need multiple dies, the overall production time will be longer.
- Gerson’s Workload: Gerson’s current order volume can influence lead times.
- Design Approval: Any delays in approving the die design can push back the production schedule.
- Finishing Processes: Additional finishing processes, such as heat treating or coating, can add to the overall time.
Typical Timeline:
- Simple Steel Rule Dies: These can sometimes be produced within one days to a week.
- More Complex Steel Rule Dies: These might take one to two weeks.
- Forged or Machined Dies: These more specialized dies can take one week or even onemonth to manufacture due to the intricate processes involved.
In summary, while producing a custom cutting die generally takes about one business days after design approval for standard dies, complexities in design or material issues ,large quantity could extend this timeline up to 30 business days or longer depending on various circumstances.
How to choose a Right Cutting Die?
Choosing the right cutting die is crucial for successful and efficient die-cutting. Here’s a comprehensive guide to help you make the best decision:
1. Material Compatibility:
- Identify the Material: Determine the type of material you’ll be cutting (paper, cardstock, fabric, leather, plastic, metal, etc.).
- Thickness and Density: Consider the material’s thickness and density. Thicker and denser materials require more robust dies.
- Material Properties: Some materials have unique properties (e.g., elasticity, abrasiveness) that might require specialized dies.
2. Die Type:
- Steel Rule Dies: Cost-effective, suitable for softer materials and simpler designs, ideal for shorter runs.
- Forged Dies: Durable, handle thicker and tougher materials, suitable for longer runs and higher pressures.
- Machined Dies: Highest accuracy, intricate designs, tight tolerances, long production runs, and thicker materials.
- Match Metal Dies: Precise cuts, thin metals, embossing.
- Rotary Dies: High-speed, continuous cutting, web materials, printing, and packaging.
- Specialty Dies: Scrap removal, nesting, corner, edge, shape, 3D, wafer-thin, coordinating, cover, layering, and embossing dies for specific purposes.
3. Design Complexity:
- Simple Shapes: Steel rule dies are often sufficient for basic shapes.
- Intricate Details: Machined dies or match metal dies are better for complex designs with fine lines.
- 3D Designs: 3D dies are needed for creating dimensional shapes.
4. Production Volume:
- Short Runs: Steel rule dies are suitable for small quantities.
- Long Runs: Forged or machined dies are more cost-effective for large production runs.
5. Die Size and Shape:
- Dimensions: Ensure the die’s size and shape match your design requirements.
- Blank Size: Consider the size of the material you’ll be using and how many pieces you can cut from it.
6. Cutting Die Machine Compatibility:
- Machine Type: Match the die type to your die-cutting machine (manual or electronic).
- Machine Capacity: Ensure the die fits within the machine’s cutting area and can handle the required pressure.
7. Cost Considerations:
- Die Cost: Get quotes from multiple manufacturers and compare prices.
- Long-Term Costs: Consider the die’s durability and how many cuts it can make before needing replacement.
8. Gerson Manufacturer:
- Experience:Gerson is a long time die manufacturer with experience in producing dies for your specific materials and applications.
- Quality:Gerson have skilled expert and workers to ensure producing high-quality dies with clean cuts and long lifespan.
- Customer Service: Gerson service team is a good communication and customer support in case you have questions or need assistance.
9. Additional Factors:
- Die Clearance: Proper clearance between the cutting edge and the die base is crucial for clean cuts.
- Cutting Profile: The grinding profile of the cutting edge should be tailored to the material being cut.
- Scrap Removal: Consider dies with built-in scrap removal for high-volume production.
10. Seeking Advice:
- Consult with Gerson: Talk to Gerson sales team to get their recommendations based on your specific needs.
- Industry Professionals: Seek advice from experienced similar industry professionals.
By carefully considering these factors, you can choose the right cutting die that meets your project requirements, budget, and production goals.
Do Gerson Have Cutting Die in Stock for Sale ?
Gerson have some standard simple cutting die in stock,Most cutting die need to custom built to meet your specific need.
Custom vs. Stock:
- Custom Orders: Gerson can design and manufacture custom cutting die to meet your exact specifications, ensuring optimal performance for your specific needs.
- Stock Models: If a standard cuttign die meets your requirements, you can purchase it directly from stock, offering a quicker delivery time.
In Conclusion:If you’re considering a cutting die, it’s advisable to reach out to our sales team to discuss your specific needs. We can provide expert guidance and ensure that you get the right cutting die for your application, whether it’s a stock cuttng die or a custom cutting die solution.
What is the Price of Gerson Cutting Die ?
The price of a cutting die can vary significantly depending on several factors. It’s not a one-size-fits-all answer, so here’s a breakdown of what influences the cost:
Factors Affecting Cutting Die Price:
- Die Type:
- Steel rule dies: These are generally the most affordable option, suitable for simpler designs and shorter runs.
- Forged dies: These are more expensive due to their durability and ability to cut thicker materials.
- Machined dies: These are the most expensive, offering the highest precision and longevity for complex designs and long production runs.
- Others dies:Gerson have many others die types .Each type ‘s price is diffenrent.
- Die Complexity: Intricate designs with fine details will cost more to produce than simple shapes.
- Size: Larger dies naturally require more material and labor, increasing the price.
- Material: The type of steel used for the die can impact the cost.
- Quantity: Ordering multiple dies at once may offer some cost savings per unit.
- Finishing: Additional processes like heat treating or specialized coatings can add to the cost.
General Price Ranges:
While it’s difficult to give exact figures, here are some rough estimates for example:
- Simple steel rule dies: $10 – $200
- Complex steel rule dies: $50 – $500
- Forged or machined dies: $100 – $500+ (can be significantly higher for very large or complex dies)
If you want to know the exact price ,please contact us for quotation.
What Information that I need to Supply for Quotation ?
When contacting Gerson or our representatives, be prepared to provide details about the type of cutting die you need, including:
- Material: What material will the die be used to cut?
- Design: Do you have a specific design or shape in mind?
- Size: What are the dimensions of the die or the cut it will make?
- Quantity: How many dies do you need?
- Shipping Address:Where will the cutting die ship to ?
With this information, We can better assist you in finding the right cutting die for your needs, whether it’s an in-stock item or a custom-made product.
What is the Price of Gerson Cutting Die ?
The lifespan of a custom cutting die can vary significantly, but with proper care and use, it can last for a considerable time. Here’s a breakdown of the factors influencing its longevity and when replacement might be necessary:
Factors Affecting Die Lifespan:
- Die Type: Different die types have varying levels of durability. Forged and machined dies are generally more robust than steel rule dies.
- Material Being Cut: Cutting abrasive or dense materials can wear down the die’s cutting edge faster than softer materials like paper or fabric.
- Die Quality: The quality of the steel used and the precision of the die’s construction play a significant role in its lifespan.
- Usage Frequency: How often the die is used directly impacts its wear and tear. High-volume production will naturally lead to more frequent replacement.
- Cutting Pressure: Applying excessive pressure can damage the die’s cutting edge, reducing its lifespan.
- Maintenance: Regular cleaning and proper storage can help prolong the die’s life.
Typical Lifespan:
- Steel Rule Dies: With proper care, these can last for thousands of cuts, sometimes even tens of thousands, especially when used on softer materials.
- Forged and Machined Dies: These more durable dies can withstand hundreds of thousands, or even millions, of cuts, particularly when used on appropriate materials and with proper maintenance.
When to Replace a Cutting Die:
- Dull Cutting Edge: If the die is no longer making clean cuts and requires excessive pressure, it’s likely time for sharpening or replacement.
- Damage: Any visible damage to the die, such as cracks, bends, or chips in the cutting edge, will necessitate replacement.
- Inconsistent Cuts: If the die is producing inconsistent cuts, even with proper pressure, it might be a sign of wear or damage.
- Reduced Efficiency: If the die is requiring more effort or time to make cuts, it could be a sign that it needs replacement.
Tips to Extend Die Lifespan:
- Use Appropriate Pressure: Avoid applying excessive pressure when cutting.
- Regular Cleaning: Clean the die after each use to remove debris or residue.
- Proper Storage: Store the die in a dry and safe place to prevent damage or corrosion.
- Sharpening: Some dies can be resharpened to extend their life. Consult with the manufacturer or a die sharpening service.
- Regular Inspection: Inspect the die regularly for signs of wear or damage.
In conclusion, the lifespan of a custom cutting die is influenced by several factors. While it’s difficult to give an exact timeframe, proper care and maintenance can significantly extend its use. When the die starts to show signs of wear, damage, or reduced efficiency, it’s best to consider replacement to ensure clean cuts and consistent results.