Clicker Press
38+ Years
Experience of Manufacturing Clicker Press
Your Best Clicker Press Manufactuer
38+ Years Manufacturing Quality
1000+ Employees Factory
Factory Direct Sale Price
Full Support on Installstion&Traning
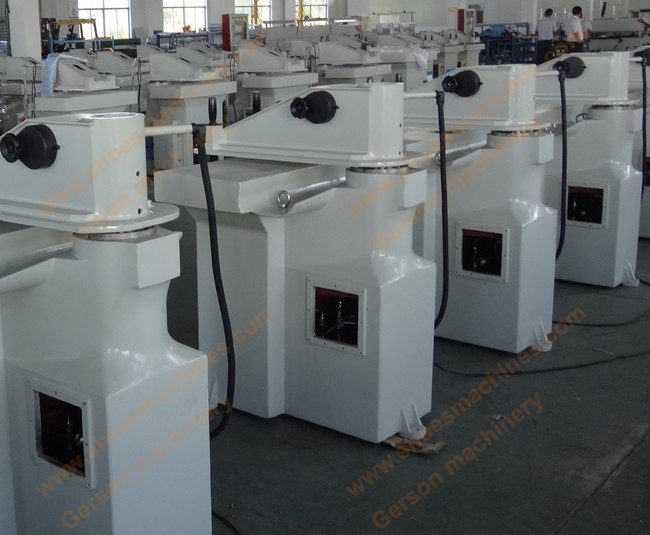
Gerson Clicker Press is a leading manufacturer of high-quality clicker presses, catering to both OEM and retail markets under its own brand name. Renowned for their versatility and reliability, Gerson clicker presses are widely used in various industries for precise cutting operations.
Gerson manufactures a diverse range of clicker press models, each tailored to specific cutting applications, offering flexibility and precision.
Gerson clicker presses are engineered with advanced hydraulic systems and premium-quality components from renowned brands. This combination ensures optimal performance, longevity, and minimal maintenance requirements.
The Gerson Swing Arm Clicker Press is a reliable and versatile hydraulic-driven, semi-automatic press. With over 38 years of manufacturing experience, Gerson has established a reputation for producing high-quality clicker presses for both OEM and own brand.
Gerson Traveling Head Clicker Press is a powerful and efficient cutting machine that features a moving head . Coupled with a large cutting table, enables high-volume production of both sheet and roll materials. Two options: manual feed and CNC autofeed .
Gerson Full Beam Clicker Press is a robust and powerful cutting machine designed for high-volume production of large material. Whether you require a single unit or a large-scale order, Gerson offers flexible manufacturing options to meet your specific needs.
Tabletop clicker press
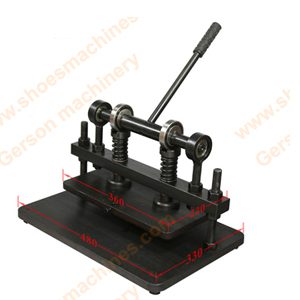
Tabletop Clicker Press is mini small size of clicker press .It is the manual clicker press using your hand power .It Can cut non-metal material with small volume.Most for Home or Shop or lab cutting jobs.Working with cutting die such as steel rule die ,forged die ,clicker die etc.,
Clicker Press Aplication
Industry | Applications | Materials |
---|---|---|
Automotive | Interior components, exterior components, under-the-hood components | Leather, fabric, foam, plastic, rubber |
Aerospace | Aircraft interior components, exterior components | Leather, fabric, composite materials, metal |
Textile and Apparel | Garments, upholstery, technical textiles | Fabric, leather, non-woven materials |
Packaging | Corrugated cardboard, paperboard, plastic films | Paper, cardboard, plastic |
Furniture | Upholstery components, wood and veneer cutting | Fabric, leather, wood, foam |
Electronics | Circuit boards, component cutting | Plastic, metal, composite materials |
Medical | Medical devices, surgical garments and drapes | Fabric, non-woven materials, plastic |
Automotive | Car mats, seat covers, steering wheel covers | Fabric, leather, rubber |
Construction | Insulation materials, gaskets and seals | Foam, rubber, plastic |
Other Industries | Footwear, leather goods, abrasives, composites, non-woven materials | Leather, fabric, rubber, plastic, composite materials, non-woven materials |
Have Question? Ask Now
State-of-the-Art Technology for Clicker Press
Gerson, a global leader in clicker press manufacturing, has revolutionized the industry with the development of its 3rd generation clicker presses. Leveraging patented hydraulic systems, these state-of-the-art machines offer unparalleled performance, efficiency, and reliability.
Key Features of Gerson’s 3rd Generation Clicker Presses:
- Lightweight Design: Reduced weight for easier operation and maintenance.
- Quiet Operation: Minimized noise pollution for a more comfortable work environment.
- Enhanced Efficiency: Optimized performance for increased productivity.
- High-Quality Components: Premium hydraulic and electrical components for superior durability and longevity.
- Fully Automatic Operation: Unattended operation for maximum efficiency and labor savings.
Gerson’s commitment to innovation and customer satisfaction drives the development of cost-effective, high-quality clicker presses that meet the evolving needs of the market. By embracing automation and advanced technologies, Gerson empowers businesses to streamline their operations and achieve greater success.
Clicker Press : Definitive Guide
(keep updating: Updated on Nov. 11th, 2024.)
Pre-1800s: Hand Cutting
Before the 1800s, die cutting relied solely on manual labor. Workers used hammers to strike cutting die molds, essentially metal templates sharpened to a cutting edge. This slow and laborious process limited production speed.
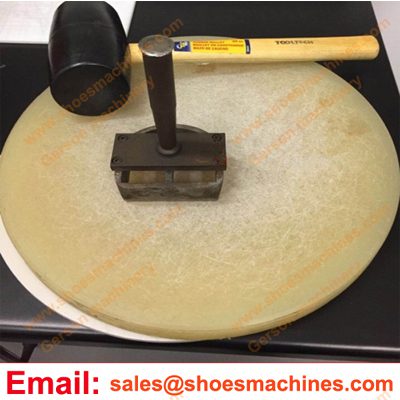
The Rise of the Clicker Press (Late 1800s):
The invention of the clicker press revolutionized die cutting. Replacing hand hammers, these machines used various power sources like manual, pneumatic, or hydraulics to press the cutting die onto the material, creating precise cuts with significantly less effort. The name “clicker” likely originated from the sound produced when the die cuts through the material.
The Clicker Press in the Shoe Industry (1900s):
Shoe factories embraced the clicker press in the early 1900s due to its speed and accuracy. It became an essential tool for cutting consistent and high-quality shoe uppers from leather.
what is the exact clicker press ?
The clicker press falls under the broader category of die cutting machines or presses. These machines utilize a cutting die to create specific shapes from various materials. However, clicker presses typically focus on non-metallic materials like leather, fabric, and rubber, powered by hydraulics.There have several kinds of cutting die molds can be used to work with clicker press.The nomal cutting die is steel rule die ,and the other is forged die .
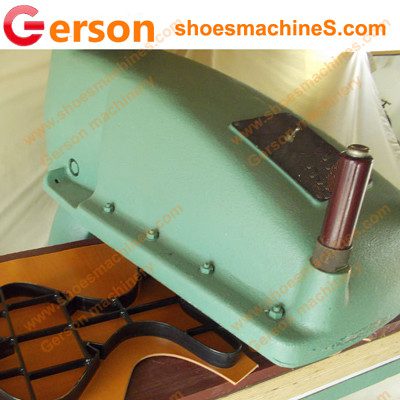
Materials and Applications:
Clicker presses can cut a wide range of materials, including:
- Felt
- Paper & Cardboard
- Sponge or Foam
- Cork
- Plastic
- Leather
- Rubber
- Fiber
- Composites
- Fabric & Textiles
They are used to create a diverse range of products, such as:
- Shoes
- Bags
- Gloves
- Packaging
- Gaskets
- Puzzles
- Slippers
- Pads & Mats
- Auto Parts
- And many more
The Future of Clicker Presses: Automation
As technology advances and labor costs rise, there’s a growing demand for automation in manufacturing. Clicker press manufacturers are responding by developing fully automatic clicker press systems. These systems can integrate into production lines, offering continuous operation and increased efficiency.
In conclusion, the clicker press has transformed die cutting from a laborious process to a cornerstone of various industries. With a focus on automation, clicker presses are poised to play an even greater role in the future of manufacturing.
Clicker Press can be used in many industries and die cutting out materials :automotive, abrasive, aerospace, carpet, composites, computers, converting, electronics, envelopes, foam, furniture, gasket, leather goods, non-woven, medical, packaging, plastic, shoes, sporting goods, textile, thermoforming, wood, paper, shoes and fabric, plastic cards and many others.
Abrasives: abrasives discs, pads, belts, strips, scouring pads, abrasive textiles and foams.
Automotive Components:Airbags,Anti-rattle components,Bodywork delivery protection,Badges and decals,Boot liners and components,Catalytic converter components,Cutting and heat sealing
Carpets, mats,Door casings,Filters,Gear lever gaiters,Gaskets and seals,Head rests,Interior trim,Insulation panels,Leather seating and trim,Number plates,Parcel shelf panels and covers,Roof liners,Seating components in fabric and leather,Steering wheel covers,Sun visors,Sound absorption panels,Wheel protectors
Carpets & Flooring:Carpet samples and swatches,Pattern cards,Carpet tiles,Vinyl samples and swatches,Automotive carpets,Car mats,Pattern books,Rubber mats,Domestic and industrial carpets,Promotional and ‘image’ flooring products,PVC and PC flooring protectors.
Clothing industry:Belts,Brassieres,Briefs,Caps,Collar interlinings,Cuffs,Gloves
Hats,Leather clothing,Lingerie,Outerwear,Protective suits,Shoulder pads,Tie linings,Underwear.
Cork:Floor tiles,Gaskets,Insulation pads,Mats,Packaging
Seals,Self adhesive pads,Table mats,Wall tiles,Washers etc.,
Plese visit our application website for more details.
Main Parts of a Clicker Press
A clicker press is a specialized machine used to cut precise shapes from various materials, primarily leather, fabric, and rubber. It consists of several key components:
- Frame: The sturdy metal frame provides the structural support for the entire machine.
- Pressing Head: This is the movable part of the machine that descends onto the material to apply pressure. It’s typically powered by hydraulic or pneumatic systems.
- Cutting Die: The cutting die is a precisely shaped metal tool that cuts the material. It’s attached to the pressing head and comes in various shapes and sizes.
- Cutting Table: A flat surface where the material to be cut is placed.
- Hydraulic System: This system generates the hydraulic pressure needed to power the pressing head. It includes a pump, reservoir, valves, and hoses.
- Control Panel: The control panel allows operators to adjust the cutting pressure, stroke length, and other parameters.
- Safety Features: These include emergency stop buttons, safety guards, and two-hand operation to prevent accidents.
Part Name | Description |
---|---|
Frame | The sturdy metal frame provides the structural support for the entire machine. |
Pressing Head | This is the movable part of the machine that descends onto the material to apply pressure. It’s typically powered by hydraulic or pneumatic systems. |
Cutting Die | The cutting die is a precisely shaped metal tool that cuts the material. It’s attached to the pressing head and comes in various shapes and sizes. |
Cutting Table | A flat surface where the material to be cut is placed. |
Hydraulic System | This system generates the hydraulic pressure needed to power the pressing head. It includes a pump, reservoir, valves, and hoses. |
Control Panel | The control panel allows operators to adjust the cutting pressure, stroke length, and other parameters. |
Safety Features | These include emergency stop buttons, safety guards, and two-hand operation to prevent accidents. |
Before You Begin:
- Hydraulic Oil: Ensure there’s sufficient hydraulic oil meeting the ISO 46 standard. Recommended brands include Mobil DTE 25 or Shell Tellus 46.
- Power Supply: Verify the correct power supply: 3-phase AC power (380V/50Hz, 220V/60Hz) or single-phase AC power (220V/50Hz, 110V/50Hz).
- Installation:
- Remove anti-rust grease.
- Place the machine on a stable surface with rubber pads.
- Connect the power supply, ensuring proper grounding.
- Turn on the power switch and check the motor’s direction.
- Run the machine idle for 5 minutes to remove air from the hydraulic system.
Initial Setup:
- Cutting Depth: Set the cutting depth knob to the minimum position.
- Die Cutter Alignment:
- Place the die cutter on the material.
- Adjust the machine head to be 10mm above the die cutter.
- Align the machine head with the center of the die cutter.
- Trial Cut:
- Press both buttons simultaneously to initiate the cutting process.
- Adjust the cutting depth as needed to achieve complete cuts.
- Avoid excessive cutting depth to prevent damage to the die cutter and machine.
Operating the Clicker Press:
- Material Placement: Place the material on the cutting pad.
- Die Cutter Positioning: Position the die cutter on the material.
- Cutting Cycle:
- Press both buttons simultaneously to activate the hydraulic press.
- The machine head descends, pressing the die cutter into the material.
- The die cuts the desired shape.
- The machine head returns to the starting position.
- Repeat the Process: Repeat steps 2 and 3 for subsequent cuts.
Safety Considerations:
- Grounding: Ensure the machine is properly grounded.
- Personal Protective Equipment (PPE): Wear safety glasses and gloves.
- Machine Operation: Only operate the machine when it’s properly set up and aligned.
- Emergency Stop: Familiarize yourself with the emergency stop button.
By following these steps and prioritizing safety, you can effectively operate your clicker press and achieve precise cutting results.
While clicker presses offer a multitude of advantages, they do have certain limitations to consider:
1. Initial Investment:
- Clicker presses, especially larger and more advanced models, involve high upfront costs for purchase and installation.
- Additional investments are needed for custom-made cutting dies.
2. Maintenance and Repair:
- Regular maintenance, including lubrication, cleaning, and hydraulic fluid management, is essential for optimal performance.
- Repairs can be costly, particularly when specialized technicians are required.
3. Physical Considerations:
- Clicker presses can be bulky and require significant floor space, potentially limiting their suitability for smaller workshops.
- Hydraulic oil operation necessitates regular maintenance, filtration, and replacement, adding to complexity.
4. Material Thickness:
- Clicker presses are typically designed for cutting relatively thin materials.
- Thicker materials can put a strain on the machine and affect cutting accuracy.
5. Die Wear and Maintenance:
- Cutting dies experience wear and tear over time, especially with frequent use.
- Regular maintenance, sharpening, or replacement of dies is crucial for optimal performance.
6. Noise and Vibration:
- Clicker presses can generate significant noise and vibration during operation, creating a noisy work environment and potentially causing damage to the machine over time.
By understanding these limitations, businesses can make informed decisions about the suitability of clicker presses for their specific needs. Additionally, strategies like preventative maintenance, proper training, and noise reduction techniques can help mitigate these challenges and maximize the benefits of clicker presses.
38+ Years of Excellence
With four decades of experience, Gerson is committed to delivering high-quality clicker presses. Our dedication to quality and customer satisfaction has earned us the trust of clients worldwide.
Custom Solutions for Your Needs
Gerson offers a diverse range of clicker press solutions to cater to various industrial needs. Whether you require a small, manual machine or a fully automated production line, we can provide custom solutions to meet your specific requirements.
In-House Die Mold Manufacturing
Our in-house die mold workshop allows us to provide comprehensive cutting solutions. We can design and manufacture custom dies to meet your exact needs.
Comprehensive Support and Services
Gerson is dedicated to providing exceptional customer service:
- Free Quotations: Receive accurate and competitive pricing for your projects.
- Superior After-Sales Service: Benefit from our prompt and reliable support.
- Responsive Customer Support: Quick response to your inquiries and concerns.
- Free Solution Consulting: Get expert advice on your cutting needs.
Built to Endure
Our clicker presses are constructed using premium-quality steel and components, ensuring durability and longevity. They are designed to withstand the rigors of daily operation.
Gerson understands that your cutting needs are unique. That’s why we offer a diverse range of clicker presses to meet the specific demands of your operation. Here’s a breakdown of our main categories:
1. Swing Arm Clicker Press (Easy Entry Type):
- Ideal for small piece cutting (cutting bed typically < 1200x600mm).
- Offers manual operation with a swinging beam for easy access and repositioning.
- Suitable for cutting forces less than 30 tons.
- Perfect for smaller workshops or low-volume production.
2. Traveling Head Clicker Press (Versatile Die Cutting):
- Features a traveling head that moves left-to-right across a larger cutting bed (from 1600x500mm and up).
- Accommodates a wider range of material sizes and cutting dies.
- Offers versatility for various cutting applications.
- Ideal for medium-volume production.
3. Full Head Clicker Press (Beam Press):
- Equipped with a full-size head matching the cutting bed dimensions.
- Designed for high or low volume production of both roll and sheet materials.
- Suitable for cutting large parts and single/multi-layered materials.
- Often features automatic sheet or roll feeding systems for increased efficiency.
- Ideal for high-volume production and industrial applications.
4. Small Tabletop Clicker Press (Benchtop):
- Compact design allows for tabletop placement.
- Perfect for very small parts and low-volume production (typically leather crafts).
- Fully manual operation with cutting force ranging from 1 to 5 tons.
- Ideal for hobbyists, small workshops, or specific craft applications.
Additional Considerations:
Gerson offers custom solutions – we can build clicker presses in various sizes and capacities to match your specific requirements. We also provide in-house die mold manufacturing to ensure a complete cutting solution.
By choosing Gerson, you gain access to reliable and high-performance clicker presses, exceptional customer support, and expert advice on your cutting needs. Contact us today to discuss your specific requirements and find the perfect clicker press for your operation!
Choosing the Right Gerson Clicker Press: A Guide
Selecting the ideal Gerson clicker press hinges on understanding your specific cutting needs. Here’s a breakdown of key factors to consider:
1. Material Properties:
- Material Type: Identify the material you’ll be cutting (leather, fabric, rubber, etc.).
- Material Format: Will you be using sheet or roll material?
- Material Dimensions: Determine the length, width, and thickness of your material.
2. Cutting Requirements:
- Part Size: Specify the maximum size of the parts you need to cut out.
- Die Size: Determine the maximum size of your cutting die.
3. Production Volume:
- Production Needs: Estimate your desired production output (low, medium, or high volume).
- Automation Level: Consider whether you require manual, semi-automatic, or fully automatic operation.
Calculating Cutting Force and Bed Size:
Once you have this information, calculate the cutting force required for your material and ensure the cutting bed size is larger than your material.
Choosing the Right Clicker Press:
By comparing the different Gerson clicker press types (Swing Arm, Traveling Head, Full Head, and Small Tabletop) based on their features and capabilities:
- Swing Arm: Ideal for small parts, manual operation, and low-volume production.
- Traveling Head: Versatile for various cutting applications and medium-volume production.
- Full Head (Beam Press): Efficient for high or low volume production of large parts and roll/sheet materials.
- Small Tabletop: Perfect for hobbyists, small workshops, or specific craft applications.
Still Unsure?
Gerson is here to help! Contact our sales department at [email protected] if you have any questions or need assistance choosing the perfect clicker press for your operation. We can provide expert advice and custom solutions to meet your unique cutting needs.
Gerson’s commitment to providing high-quality clicker press solutions extends beyond borders. We have a strong global presence, exporting our products to numerous countries worldwide.
Here are some of the countries where Gerson clicker presses are trusted and used:
- Europe: Austria, Belgium, Czech Republic, Denmark, Finland, France, Germany, Greece, Hungary, Iceland, Ireland, Italy, Latvia, Lithuania, Netherlands, Norway, Poland, Portugal, Romania, Russia, Spain, Sweden, Switzerland, Turkey, Ukraine, UK
- North America: Canada, USA, Mexico
- South America: Brazil, Chile, Colombia, Costa Rica, Ecuador, Peru
- Asia: China, India, Indonesia, Japan, Korea, Malaysia, Philippines, Singapore, Thailand, Vietnam
- Middle East: Iran, Israel, Saudi Arabia, UAE
- Africa: South Africa
- Oceania: Australia, New Zealand
No matter where you are located, Gerson can provide you with the right clicker press solution. Contact us today to learn more about our global reach and how we can assist
Gerson Clicker Presses are renowned for their precision, durability, and efficiency. Here are some of their key features:
Precision Cutting
- Accurate Cuts: Gerson presses are designed to deliver precise cuts, minimizing waste and maximizing material utilization.
- Consistent Quality: Consistent cutting pressure and alignment ensure uniform results.
Durability and Reliability
- Robust Construction: Built with high-quality materials and components for long-lasting performance.
- Durable Hydraulic System: Reliable hydraulic systems provide consistent power and accuracy.
- Low Maintenance: Minimal downtime due to robust design and easy maintenance.
Safety Features
- Two-Hand Operation: Ensures safe operation and prevents accidental activation.
- Emergency Stop: Quick and easy access to emergency stop buttons.
- Safety Guards: Protect operators from moving parts.
Customization Options
- Tailored Solutions: Gerson can customize presses to meet specific needs, including cutting force, bed size, and automation level.
- Modular Design: Allows for easy customization and future upgrades.
User-Friendly Design
- Intuitive Controls: Simple and easy-to-use controls for efficient operation.
- Ergonomic Design: Reduces operator fatigue and improves productivity.
By incorporating these features, Gerson Clicker Presses have become a preferred choice for businesses across various industries, including footwear, apparel, automotive, and more.
Gerson offers a high degree of customization for its clicker presses, ensuring they meet the exact needs of your production process. When considering a custom-built clicker press, Gerson will work closely with you to determine the following:
- Material Type: Specify the materials you’ll be cutting (leather, fabric, rubber, etc.).
- Material and Die Dimensions: Provide information on the size of your materials and cutting dies.
- Specific Requirements: Share any unique needs or features you desire in your clicker press.
Gerson’s expertise allows them to manufacture clicker presses with a wide range of cutting forces, typically between 8 and 500 tons. This flexibility ensures that you’ll receive a machine that is perfectly suited to your specific applications.
By working closely with Gerson, you can obtain a custom clicker press that delivers optimal performance, efficiency, and durability.
Yes, Gerson Accepts Orders for Single Clicker Presses
Gerson, with its extensive experience in clicker press manufacturing, is equipped to handle orders of any size, including single-unit purchases. Our diverse product range and commitment to customer satisfaction ensure that even small-scale customers can benefit from our high-quality machines.
Gerson likely sees value in even single-unit orders,Here’s a breakdown of why:
- Building Customer Relationships: Even a small order can be a starting point for a long-lasting business relationship. Satisfied customers can become repeat customers or refer Gerson to others.
- Market Penetration: Each new customer, regardless of order size, helps Gerson expand its market reach and brand recognition.
- Product Testing and Feedback: Single-unit orders can provide valuable feedback on product performance and customer satisfaction, which can help Gerson improve future products and services.
- Potential for Upselling and Cross-Selling: A single-unit order can be an opportunity to introduce customers to additional products or services, such as spare parts, maintenance contracts, or future machine upgrades.
By valuing every customer, regardless of order size, Gerson can foster long-term relationships and drive business growth.So ,Whether you’re a small business or a large-scale manufacturer, Gerson can provide you with the right clicker press solution.
Regular Models: Gerson typically maintains a stock of their standard clicker press models for faster delivery.
Custom Presses: Clicker presses built to specific requirements may require production and might not be readily available in stock.
To confirm current stock availability:
Please contact Gerson’s sales team directly. They can provide the most up-to-date information on specific models and lead times for custom builds.
To ensure your Gerson Clicker Press operates efficiently and lasts for years, follow these essential maintenance tips:
Daily Maintenance
- Cleanliness: Wipe down the machine to remove dirt, debris, and material scraps.
- Die Inspection: Visually inspect dies for wear and damage. Replace or repair damaged dies promptly.
- Hydraulic Fluid Check: Ensure the hydraulic fluid level is correct and free of contaminants.
Weekly Maintenance
- Lubrication: Apply lubricant to moving parts as recommended by the manufacturer.
- Electrical Check: Inspect electrical components for loose connections or signs of damage.
- Safety Checks: Verify the functionality of safety features, such as emergency stop buttons and guards.
Monthly Maintenance
- Hydraulic System Inspection: Check for leaks, air bubbles, and contamination in the hydraulic fluid.
- Filter Cleaning: Clean or replace filters as needed to maintain optimal performance.
- Belt and Pulley Inspection: Inspect belts and pulleys for wear, tension, and alignment.
Annual Maintenance
- Professional Inspection: Schedule a comprehensive inspection by a qualified technician.
- Major Component Replacement: Replace worn-out components like seals, gaskets, and hoses.
- Calibration: Ensure accurate cutting and pressure settings through calibration.
Additional Tips:
- Operator Training: Ensure operators are well-trained to use the machine safely and efficiently.
- Clean Work Environment: A clean workspace minimizes the risk of contamination and damage to the machine.
- Regular Software Updates: If applicable, keep the machine’s software up-to-date.
- Preventive Maintenance: Implement a preventive maintenance schedule to identify and address potential issues early.
By following these maintenance guidelines, you can significantly extend the lifespan of your Gerson Clicker Press and ensure its continued performance.
Gerson offers a robust training and support program to ensure optimal performance and longevity of its clicker presses. This includes:
On-Site Training
- Operator Training: Gerson provides in-depth training to operators on how to safely and efficiently operate the clicker press. This includes instruction on:
- Proper machine startup and shutdown procedures
- Die setup and adjustment
- Material handling and feeding techniques
- Troubleshooting common issues
- Maintenance Training: Gerson’s technicians can train maintenance personnel on routine maintenance tasks, such as:
- Lubrication
- Cleaning
- Hydraulic system checks
- Electrical component inspection
- Die maintenance and sharpening
Remote Support
- Technical Assistance: Gerson offers remote technical support via phone or email to address any questions or issues that may arise.
- Troubleshooting Guidance: Experienced technicians can provide step-by-step troubleshooting advice to help diagnose and resolve problems.
Spare Parts and Accessories
- Genuine Parts: Gerson provides original spare parts to ensure optimal performance and longevity.
- Quick Delivery: Efficient supply chain management ensures timely delivery of spare parts.
By providing comprehensive training and support, Gerson empowers its customers to maximize the productivity and efficiency of Our clicker presses.