Gerson Beater Addition Gaskets Die Cutting Machine is a a specialized die-cutting machine ideal for cutting gasket materials, including beater add gaskets.
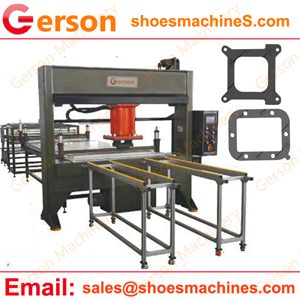
This versatile machine is capable of handling a wide range of gasket materials:
Gasket Material | Specific gasket Material Name |
---|---|
Elastomers | Nitrile (NBR), Buna-N, SBR, EPDM, Viton® (FKM), Hypalon, Aflas®, Natural Rubber, Neoprene,Butyl Rubber, |
Fibers and Textiles | Aramid Fiber, Cellulose Fiber, Fiberglass Cloth, Grafoil®, Kevlar, Mica, Vegetable Fiber, Wire Mesh |
Plastics and Resins | Chemraz®, EVA, Lexan, Phenolic, Polyurethane, PVC, Teflon®, UHMW |
Composites and Laminates | Cork and Rubber, FRP, Laminated Material, Rubberized Fiberglass Cloth, Silicone Rubber |
Other Materials | Fish Paper, Vulcanized Fiber, Soft Goods, Gylon, Klinger, Taskline,Thermoseal |
Key Features and Benefits:
- Hydraulic Operation: Delivers controlled cutting force for consistent and high-quality results.
- Versatile Material Handling: Accommodates various materials and thicknesses, from delicate thin to thick gasket material sheets or roll.
- Advanced Automation: Offers CNC integration for precise cutting patterns and automated material handling, boosting productivity.For smaller-scale production needs, Gerson also offers manual traveling head presses, providing a cost-effective solution for cutting gasket materials.
- Enhanced Safety: Incorporates safety features like light curtains and emergency stop buttons to protect operators.
- User-Friendly Controls: Intuitive interfaces and customizable settings simplify operation and maintenance.
- Customizable Options: To meet the unique needs of various industries and production processes, Gerson offer a wide range of customization options:
- Cutting Head Size: Available in different sizes to accommodate various material widths and thicknesses.
- Feeding Systems: Choose from sheet feeders or roll feeders to suit your material supply method.
- Cutting Force: Adjustable cutting force to handle a broad range of materials, from soft to hard.
- Working Table Size: Customizable table sizes to accommodate different workpiece dimensions.
- Specialized Cutting Die Tools: Custom-designed cutting dies for intricate shapes and precise cuts.
- Control Systems: Advanced control systems for precise operation, monitoring, and data analysis.
- Improved Efficiency: Streamlines production processes with automated material feeding and unloading systems.
Core Components and Functions:
- Traveling Head: The cutting head moves across the material, enabling intricate cutting patterns and precise shapes.
- Hydraulic System: Provides the necessary force for cutting, ensuring consistent pressure distribution.
- Control System: Allows for precise control over cutting speed, depth, and pattern.
- Cutting Tools: A variety of cutting tools are available to accommodate different materials and cutting styles.
Specification :
Model | GRM(A)-25T to 200T |
Max cutting force(T) | From 25 Tons to 200 Tons |
Range between working table | 50-240mm (Upper to Bottom Table) |
Stroke Adjustment | 0-170mm |
Cutting table width(mm) | 1800~2500mm or more |
Based on your material and die | |
Example: 1600X600mm etc., | |
Cutting Head
Movable trolley |
500×500 to 1000x1000mm |
Motor power | 3kw to 22KW |
Electric Power | 220V/380V/415V,50-60hz etc., |
Machine Net weight (KG) | 1600 to 16500 |
1700 to 17500 |
By harnessing the power of hydraulics and advanced automation, automatic traveling head presses offer significant advantages in terms of productivity, accuracy, and safety.
Gerson traveling head press have become indispensable tools in modern manufacturing, particularly for industries requiring precise cutting and stamping operations. Their versatility, efficiency, and precision make them ideal for producing a wide range of components, including gaskets.
By offering customizable options such as cutting head size, feeding systems, and cutting force, these machines can be tailored to meet specific production requirements. This flexibility, combined with advanced control systems, ensures optimal performance and product quality.
As technology continues to evolve, we can anticipate even more innovative and efficient automatic traveling head presses to emerge, further revolutionizing manufacturing processes.